自动测试仪MSA模板
使用EXCEL的公式计算功能,自动完成1人5次10工件的GRR分析工作,使用时,只需输入测量数据及其相关信息即可!
半导体制造商提高质量和产量的 4 个步骤
半导体制造不仅是技术最先进的行业之一,而且也是成本最密集的行业之一。随着基于半导体的设备在从个人电脑到电话和汽车的一切事物中变得司空见惯,需求持续增长。随着数量的增加,对更强大的质量计划的需求也在增加。虽然大多数制造商都在使用 Minitab 等统计软件来解决某些问题,但仍有机会扩大其范围并提供更多价值。
半导体制造业往往比其他行业平均收集更多的数据。这意味着您可以更轻松地将数据以不同的方式发挥作用,例如:
使用测量系统分析最大限度地减少生产中的变化
使用量具 R&R 和方差分析等工具来确定测量系统的变化至关重要,尤其是对于半导体制造而言。为确保规格能够得到保证,测量的可重复性和再现性需要相对于测量的规格公差较小。 Minitab 的新测量系统分析 模块使各级从业人员能够轻松评估测量系统的变异、偏差和稳定性。
使用统计过程控制来提高产量并避免制造过程中的浪费
使用控制图和能力分析来测量关键特性,如晶圆厚度、沉积速率(晶圆表面沉积材料作为薄层以包含电气特性的速率)、终点时间(检测最准确的停止时间蚀刻工艺,以避免蚀刻过度或蚀刻不足)等将有助于确保您的工艺和设备处于可控状态。如果您已经在使用 SPC 方法,使用Minitab的 下一代统计过程控制可以帮助您改进技术并实现实时节省。
使用实验设计改进制造工艺
由于半导体制造由多个复杂的过程组成,即使是最有经验和能力的工程师也不一定知道制造设备的最佳设置。即使已知最佳设置,新技术也会不断被采用,从而引入未知情况和新问题。实验设计帮助工程师建立一个综合模型,以帮助非常准确地理解系统的工作原理。 通过阅读这篇博文,了解更多关于 DOE 的实际操作,帮助提高一个制造商抛光过程的均匀度,或者通过观看本次网络研讨会,了解更多关于 DOE 的总体信息。
使用机器学习进行硅后验证
与进行测量并做出通过/失败决策的生产测试不同,在硅后验证中,您需要非常详细地了解设备在各种操作条件下的行为。使用机器学习,您可以更好地了解设备的输入如何影响输出并找到它们之间隐藏的关系和复杂性。借助Minitab 的预测分析模块,您可以构建稳健的预测模型或使用我们的可变重要性图表等工具来突出显示影响性能的最关键输入。
收起阅读 »
半导体制造业往往比其他行业平均收集更多的数据。这意味着您可以更轻松地将数据以不同的方式发挥作用,例如:
使用测量系统分析最大限度地减少生产中的变化
使用量具 R&R 和方差分析等工具来确定测量系统的变化至关重要,尤其是对于半导体制造而言。为确保规格能够得到保证,测量的可重复性和再现性需要相对于测量的规格公差较小。 Minitab 的新测量系统分析 模块使各级从业人员能够轻松评估测量系统的变异、偏差和稳定性。
使用统计过程控制来提高产量并避免制造过程中的浪费
使用控制图和能力分析来测量关键特性,如晶圆厚度、沉积速率(晶圆表面沉积材料作为薄层以包含电气特性的速率)、终点时间(检测最准确的停止时间蚀刻工艺,以避免蚀刻过度或蚀刻不足)等将有助于确保您的工艺和设备处于可控状态。如果您已经在使用 SPC 方法,使用Minitab的 下一代统计过程控制可以帮助您改进技术并实现实时节省。
使用实验设计改进制造工艺
由于半导体制造由多个复杂的过程组成,即使是最有经验和能力的工程师也不一定知道制造设备的最佳设置。即使已知最佳设置,新技术也会不断被采用,从而引入未知情况和新问题。实验设计帮助工程师建立一个综合模型,以帮助非常准确地理解系统的工作原理。 通过阅读这篇博文,了解更多关于 DOE 的实际操作,帮助提高一个制造商抛光过程的均匀度,或者通过观看本次网络研讨会,了解更多关于 DOE 的总体信息。
使用机器学习进行硅后验证
与进行测量并做出通过/失败决策的生产测试不同,在硅后验证中,您需要非常详细地了解设备在各种操作条件下的行为。使用机器学习,您可以更好地了解设备的输入如何影响输出并找到它们之间隐藏的关系和复杂性。借助Minitab 的预测分析模块,您可以构建稳健的预测模型或使用我们的可变重要性图表等工具来突出显示影响性能的最关键输入。
收起阅读 »
MSA GRR研究时的样本问题及解决策略
按照AIAG 《MSA参考手册》第四版中第95页中的要求,GRR(测量系统的重复性和再现性)研究时应当“取得一个能够代表过程变差实际或预期范围的样本”。我相信那些参考过该手册做过MSA的朋友已经意识到了:这个要求,在新产品开发的阶段是难以满足的!我们先了解一下GRR的3个指标:
其中,
可见,%GRR对过程总变差的指标P/TV,以及对零件变差的指标ndc(分辨率)均会受到零件间变差σp的影响。因此,这就是为什么《MSA参考手册》规定用作评估样本的零件应能代表实际的过程变差或预期变差,这样评价出的测量系统,才能够适用于当前产品的测量。
然而,在新产品开发阶段,测量系统和制造过程是同步开发的,在测量系统的预验收阶段,是没有那么多的产品样本供我们测量的,也就是2-3个样品,甚至还不能满足GRR评估时最少的样本数量5个的要求(注:MSA参考手册中的要求得到至少45个测量值,以确保评估结果的置信度)。
到了测量系统的最终验收阶段,虽然可以满足GRR的样本量的要求,但是这个时候的样本之间的变差也是相当大的,因为过程还远未达到量产时的稳定状态和能力水平!而我们开发的测量系统,是为了用于量产以后的测量的,如果仅仅使用试生产时的产品作为样本来评价GRR,它的这两个指标即使满足了要求(P/TV<=10%,ndc>=5),在量产后,也很可能会因零件变差的减小而不再满足要求的!但是量产后,量具及测量工装已经定型和安装到位了,已经不能推倒重来了!
那么,如何才能避免这种尴尬和被动的局面呢?
在测量系统的预验收阶段,如果用于样本的零件数量不能满足5个的要求,我们就只能评估它的量具能力Cgk了。评价Cgk时,只使用一个样本进行重复测量就可以了。Cgk可以反应测量系统的重复性和偏倚误差,Cg反应测量系统重复性误差,以及在这两个方面满足产品公差要求的能力,如下图所示,
等到了测量系统的最终验证阶段,我们可以使用量产后过程能力指数CP的目标值来导出过程总变差的目标值,使用这个目标值来评估测量系统是否满足预期的测量精度要求,即:
这样,我们可以得到期望的过程总变差的目标值σc,在把试生产时的样品测量完成后,再将这个σc代入到GRR的上述两个指标的计算公式中,用它评价出来的测量系统的指标,就可以适用于量产后过程稳定时产品的测量。
这样,我们就可以成功地避免上面所讲的尴尬和被动的局面了。
但是,如果量产后实际的过程能力相当高,远高于过程能力指数CPK的目标值(如1.33),即过程总变差可能是很小,这样的话,P/TV和ndc的指标值就有可能不能满足要求了(<=10%和>=5)。那么我们还应当升级测量系统吗?升级测量系统,就意味着更换测量仪器,就需要更高的投资!
我在此的看法是:可以根据企业自己的情况来决定是否升级、如何升级。可以分为以下几种情况来考虑:
1、首先来判断指标P/TV和ndc不满足要求(如<=10%),真的是由于过程能力提高了,还是测量系统变差了。判断的方法是:使用GRR对公差的指标P/T,如果这个指标的值相比之前的评估没有增加,那么就说明测量系统没变,而是由于过程能力提高了。
2、如果本来用的就是精度很高的测量仪器,如CMM、OMM等,这样就基本不存在测量系统精度不满足过程能力提高的情况;
3、如果测量系统的指标不能满足实际过程能力的提高,且测量的数据不做统计分析如SPC控制图等,只用于检测产品合不合格,就可以暂时不用升级测量系统。
4、如果测量系统的指标不能满足实际过程能力的提高,但必须要做控制图来监控生产过程,那么就应当升级测量系统。如果不升级测量系统,其分辨率就不能满足控制图的要求,做出的控制图就会存在下面的问题:
5、如果实际的过程能力达到了非常高的水平,如CPK=3.0,那么,如果要求测量系统来适应过程能力,就可能需要巨额的投入去采购高端的测量仪器,管理层不太可能批准的!这个时候,我们甚至连控制图也不做了!
但是,无论是上述哪种情形,我们必须坚守住过程能力目标值这个“底线”,以及在该目标值下对应的测量系统的精度水平。
如何去坚守这个”底线“呢?就是按照MSA的计划,定期抽取产品样本进行测量,使用过程变差的目标值(用CP的目标值推出来)来对测量系统进行评估,看看测量系统有没有变差。 收起阅读 »
其中,
可见,%GRR对过程总变差的指标P/TV,以及对零件变差的指标ndc(分辨率)均会受到零件间变差σp的影响。因此,这就是为什么《MSA参考手册》规定用作评估样本的零件应能代表实际的过程变差或预期变差,这样评价出的测量系统,才能够适用于当前产品的测量。
然而,在新产品开发阶段,测量系统和制造过程是同步开发的,在测量系统的预验收阶段,是没有那么多的产品样本供我们测量的,也就是2-3个样品,甚至还不能满足GRR评估时最少的样本数量5个的要求(注:MSA参考手册中的要求得到至少45个测量值,以确保评估结果的置信度)。
到了测量系统的最终验收阶段,虽然可以满足GRR的样本量的要求,但是这个时候的样本之间的变差也是相当大的,因为过程还远未达到量产时的稳定状态和能力水平!而我们开发的测量系统,是为了用于量产以后的测量的,如果仅仅使用试生产时的产品作为样本来评价GRR,它的这两个指标即使满足了要求(P/TV<=10%,ndc>=5),在量产后,也很可能会因零件变差的减小而不再满足要求的!但是量产后,量具及测量工装已经定型和安装到位了,已经不能推倒重来了!
那么,如何才能避免这种尴尬和被动的局面呢?
在测量系统的预验收阶段,如果用于样本的零件数量不能满足5个的要求,我们就只能评估它的量具能力Cgk了。评价Cgk时,只使用一个样本进行重复测量就可以了。Cgk可以反应测量系统的重复性和偏倚误差,Cg反应测量系统重复性误差,以及在这两个方面满足产品公差要求的能力,如下图所示,
等到了测量系统的最终验证阶段,我们可以使用量产后过程能力指数CP的目标值来导出过程总变差的目标值,使用这个目标值来评估测量系统是否满足预期的测量精度要求,即:
这样,我们可以得到期望的过程总变差的目标值σc,在把试生产时的样品测量完成后,再将这个σc代入到GRR的上述两个指标的计算公式中,用它评价出来的测量系统的指标,就可以适用于量产后过程稳定时产品的测量。
这样,我们就可以成功地避免上面所讲的尴尬和被动的局面了。
但是,如果量产后实际的过程能力相当高,远高于过程能力指数CPK的目标值(如1.33),即过程总变差可能是很小,这样的话,P/TV和ndc的指标值就有可能不能满足要求了(<=10%和>=5)。那么我们还应当升级测量系统吗?升级测量系统,就意味着更换测量仪器,就需要更高的投资!
我在此的看法是:可以根据企业自己的情况来决定是否升级、如何升级。可以分为以下几种情况来考虑:
1、首先来判断指标P/TV和ndc不满足要求(如<=10%),真的是由于过程能力提高了,还是测量系统变差了。判断的方法是:使用GRR对公差的指标P/T,如果这个指标的值相比之前的评估没有增加,那么就说明测量系统没变,而是由于过程能力提高了。
2、如果本来用的就是精度很高的测量仪器,如CMM、OMM等,这样就基本不存在测量系统精度不满足过程能力提高的情况;
3、如果测量系统的指标不能满足实际过程能力的提高,且测量的数据不做统计分析如SPC控制图等,只用于检测产品合不合格,就可以暂时不用升级测量系统。
4、如果测量系统的指标不能满足实际过程能力的提高,但必须要做控制图来监控生产过程,那么就应当升级测量系统。如果不升级测量系统,其分辨率就不能满足控制图的要求,做出的控制图就会存在下面的问题:
5、如果实际的过程能力达到了非常高的水平,如CPK=3.0,那么,如果要求测量系统来适应过程能力,就可能需要巨额的投入去采购高端的测量仪器,管理层不太可能批准的!这个时候,我们甚至连控制图也不做了!
但是,无论是上述哪种情形,我们必须坚守住过程能力目标值这个“底线”,以及在该目标值下对应的测量系统的精度水平。
如何去坚守这个”底线“呢?就是按照MSA的计划,定期抽取产品样本进行测量,使用过程变差的目标值(用CP的目标值推出来)来对测量系统进行评估,看看测量系统有没有变差。 收起阅读 »
MSA GRR研究时的样本问题及解决策略
按照AIAG 《MSA参考手册》第四版中第95页中的要求,GRR(测量系统的重复性和再现性)研究时应当“取得一个能够代表过程变差实际或预期范围的样本”。我相信那些参考过该手册做过MSA的朋友已经意识到了:这个要求,在新产品开发的阶段是难以满足的!我们先了解一下GRR的3个指标:
其中,
可见,%GRR对过程总变差的指标P/TV,以及对零件变差的指标ndc(分辨率)均会受到零件间变差σp的影响。因此,这就是为什么《MSA参考手册》规定用作评估样本的零件应能代表实际的过程变差或预期变差,这样评价出的测量系统,才能够适用于当前产品的测量。
然而,在新产品开发阶段,测量系统和制造过程是同步开发的,在测量系统的预验收阶段,是没有那么多的产品样本供我们测量的,也就是2-3个样品,甚至还不能满足GRR评估时最少的样本数量5个的要求(注:MSA参考手册中的要求得到至少45个测量值,以确保评估结果的置信度)。
到了测量系统的最终验收阶段,虽然可以满足GRR的样本量的要求,但是这个时候的样本之间的变差也是相当大的,因为过程还远未达到量产时的稳定状态和能力水平!而我们开发的测量系统,是为了用于量产以后的测量的,如果仅仅使用试生产时的产品作为样本来评价GRR,它的这两个指标即使满足了要求(P/TV<=10%,ndc>=5),在量产后,也很可能会因零件变差的减小而不再满足要求的!但是量产后,量具及测量工装已经定型和安装到位了,已经不能推倒重来了!
那么,如何才能避免这种尴尬和被动的局面呢?
在测量系统的预验收阶段,如果用于样本的零件数量不能满足5个的要求,我们就只能评估它的量具能力Cgk了。评价Cgk时,只使用一个样本进行重复测量就可以了。Cgk可以反应测量系统的重复性和偏倚误差,Cg反应测量系统重复性误差,以及在这两个方面满足产品公差要求的能力,如下图所示,
等到了测量系统的最终验证阶段,我们可以使用量产后过程能力指数CP的目标值来导出过程总变差的目标值,使用这个目标值来评估测量系统是否满足预期的测量精度要求,即:
这样,我们可以得到期望的过程总变差的目标值σc,在把试生产时的样品测量完成后,再将这个σc代入到GRR的上述两个指标的计算公式中,用它评价出来的测量系统的指标,就可以适用于量产后过程稳定时产品的测量。
这样,我们就可以成功地避免上面所讲的尴尬和被动的局面了。
但是,如果量产后实际的过程能力相当高,远高于过程能力指数CPK的目标值(如1.33),即过程总变差可能是很小,这样的话,P/TV和ndc的指标值就有可能不能满足要求了(<=10%和>=5)。那么我们还应当升级测量系统吗?升级测量系统,就意味着更换测量仪器,就需要更高的投资!
我在此的看法是:可以根据企业自己的情况来决定是否升级、如何升级。可以分为以下几种情况来考虑:
1、首先来判断指标P/TV和ndc不满足要求(如<=10%),真的是由于过程能力提高了,还是测量系统变差了。判断的方法是:使用GRR对公差的指标P/T,如果这个指标的值相比之前的评估没有增加,那么就说明测量系统没变,而是由于过程能力提高了。
2、如果本来用的就是精度很高的测量仪器,如CMM、OMM等,这样就基本不存在测量系统精度不满足过程能力提高的情况;
3、如果测量系统的指标不能满足实际过程能力的提高,且测量的数据不做统计分析如SPC控制图等,只用于检测产品合不合格,就可以暂时不用升级测量系统。
4、如果测量系统的指标不能满足实际过程能力的提高,但必须要做控制图来监控生产过程,那么就应当升级测量系统。如果不升级测量系统,其分辨率就不能满足控制图的要求,做出的控制图就会存在下面的问题:
5、如果实际的过程能力达到了非常高的水平,如CPK=3.0,那么,如果要求测量系统来适应过程能力,就可能需要巨额的投入去采购高端的测量仪器,管理层不太可能批准的!这个时候,我们甚至连控制图也不做了!
但是,无论是上述哪种情形,我们必须坚守住过程能力目标值这个“底线”,以及在该目标值下对应的测量系统的精度水平。
如何去坚守这个“底线”呢?就是按照MSA的计划,定期抽取产品样本进行测量,使用过程变差的目标值(用CP的目标值推出来)来对测量系统进行评估,看看测量系统有没有变差。 收起阅读 »
其中,
可见,%GRR对过程总变差的指标P/TV,以及对零件变差的指标ndc(分辨率)均会受到零件间变差σp的影响。因此,这就是为什么《MSA参考手册》规定用作评估样本的零件应能代表实际的过程变差或预期变差,这样评价出的测量系统,才能够适用于当前产品的测量。
然而,在新产品开发阶段,测量系统和制造过程是同步开发的,在测量系统的预验收阶段,是没有那么多的产品样本供我们测量的,也就是2-3个样品,甚至还不能满足GRR评估时最少的样本数量5个的要求(注:MSA参考手册中的要求得到至少45个测量值,以确保评估结果的置信度)。
到了测量系统的最终验收阶段,虽然可以满足GRR的样本量的要求,但是这个时候的样本之间的变差也是相当大的,因为过程还远未达到量产时的稳定状态和能力水平!而我们开发的测量系统,是为了用于量产以后的测量的,如果仅仅使用试生产时的产品作为样本来评价GRR,它的这两个指标即使满足了要求(P/TV<=10%,ndc>=5),在量产后,也很可能会因零件变差的减小而不再满足要求的!但是量产后,量具及测量工装已经定型和安装到位了,已经不能推倒重来了!
那么,如何才能避免这种尴尬和被动的局面呢?
在测量系统的预验收阶段,如果用于样本的零件数量不能满足5个的要求,我们就只能评估它的量具能力Cgk了。评价Cgk时,只使用一个样本进行重复测量就可以了。Cgk可以反应测量系统的重复性和偏倚误差,Cg反应测量系统重复性误差,以及在这两个方面满足产品公差要求的能力,如下图所示,
等到了测量系统的最终验证阶段,我们可以使用量产后过程能力指数CP的目标值来导出过程总变差的目标值,使用这个目标值来评估测量系统是否满足预期的测量精度要求,即:
这样,我们可以得到期望的过程总变差的目标值σc,在把试生产时的样品测量完成后,再将这个σc代入到GRR的上述两个指标的计算公式中,用它评价出来的测量系统的指标,就可以适用于量产后过程稳定时产品的测量。
这样,我们就可以成功地避免上面所讲的尴尬和被动的局面了。
但是,如果量产后实际的过程能力相当高,远高于过程能力指数CPK的目标值(如1.33),即过程总变差可能是很小,这样的话,P/TV和ndc的指标值就有可能不能满足要求了(<=10%和>=5)。那么我们还应当升级测量系统吗?升级测量系统,就意味着更换测量仪器,就需要更高的投资!
我在此的看法是:可以根据企业自己的情况来决定是否升级、如何升级。可以分为以下几种情况来考虑:
1、首先来判断指标P/TV和ndc不满足要求(如<=10%),真的是由于过程能力提高了,还是测量系统变差了。判断的方法是:使用GRR对公差的指标P/T,如果这个指标的值相比之前的评估没有增加,那么就说明测量系统没变,而是由于过程能力提高了。
2、如果本来用的就是精度很高的测量仪器,如CMM、OMM等,这样就基本不存在测量系统精度不满足过程能力提高的情况;
3、如果测量系统的指标不能满足实际过程能力的提高,且测量的数据不做统计分析如SPC控制图等,只用于检测产品合不合格,就可以暂时不用升级测量系统。
4、如果测量系统的指标不能满足实际过程能力的提高,但必须要做控制图来监控生产过程,那么就应当升级测量系统。如果不升级测量系统,其分辨率就不能满足控制图的要求,做出的控制图就会存在下面的问题:
5、如果实际的过程能力达到了非常高的水平,如CPK=3.0,那么,如果要求测量系统来适应过程能力,就可能需要巨额的投入去采购高端的测量仪器,管理层不太可能批准的!这个时候,我们甚至连控制图也不做了!
但是,无论是上述哪种情形,我们必须坚守住过程能力目标值这个“底线”,以及在该目标值下对应的测量系统的精度水平。
如何去坚守这个“底线”呢?就是按照MSA的计划,定期抽取产品样本进行测量,使用过程变差的目标值(用CP的目标值推出来)来对测量系统进行评估,看看测量系统有没有变差。 收起阅读 »
制造业面临的一个主要问题:稳定性!
任何不稳定的行为和过程都会给客户带来质量问题和干扰。为了防止出现问题,部件必须采用稳定的过程制造,而且制造过程必须符合预期规范并高于客户满意度。
然而,制造过程中通常有多个连续的步骤。即使一个步骤出现轻微偏差也可能影响整条生产线。为了帮助您更好地理解制造稳定性,本篇文章将:
1. 探索对改进生产稳定性起阻碍作用的常见威胁
2. 介绍如何克服这些威胁
3. 使您能够使用 Minitab Engage™运行自己的改进项目
让我们从制造稳定性的简要概述开始。
什么是生产稳定性?
生产稳定性是组织在任何给定时间段内保持其生产水平的能力。
什么是精益制造稳定性?
在精益制造中,稳定性一词用于描述可以使用相同的材料、设备和人员重复进行的生产过程。如果拥有稳定的过程,则将在可预测的时间范围内以最少的浪费支持高质量的输出。稳定性与变异相反,变异会对上述能力产生负面影响。
如何改进制造业中的生产稳定性
下面,我们将概述一些对稳定性的常见威胁,以及为贵组织解决这些威胁的方法。
威胁 1:标准化与人性
跨团队产生想法、合作开发数据驱动型解决方案以及使用强健的方法来识别变异源都需要经过验证的标准化工具。
不幸的是,人类的一些自然倾向会给团队带来问题和混淆:
• 在定义问题和范围之前跳转到解决方案。
• 在完成当前项目并解决手头问题之前,过快地转移到下一个问题。
• 主要基于主观臆测(而不是数据和铁证)提出潜在的解决方案。
• 开始分析数据而不检查其质量(包括数据的收集和测量方式)。
为了避免这些常见的缺陷,实施具有久经验证的可靠记录的方法将有助于团队分享共同的观点。例如,为了帮助您有效地解决复杂问题,DMAIC 方法具有以下标准化阶段:定义、测量、分析、改进和控制。它将问题划分为更便于管理的较小阶段,并使用包含多种强大工具的工具箱。我们最新的端到端改进解决方案 Minitab Engage 中提供了 DMAIC 以及其他问题解决方法。
确保项目遍历方法的所有步骤需要遵循一定的准则。幸运的是,Minitab Engage 通过阶段审查和审批、控制台报告和电子邮件通知随时跟踪您的项目。
威胁 2:公差
通常不可能完全消除过程中的变异。难以管理的紧公差通常会导致组织的最终成本增加。如果(在设计阶段)从一开始就没有充分考虑到这种威胁,制造厂家将难以实现其预期绩效。
随着供应链在全球范围内不断扩张,供应商力求完成更大的订单,供应商排名的一个关键标准是是否有能力保持在关键参数的规格限内。
威胁 3:稳定性 = 竞争优势
公司不断鼓励其供应商更好地控制其过程的稳定性。每当不稳定性在供应商之间传递并最终在客户之间传递时,因此导致的成本就会增加。在制造过程中很晚才检测到缺陷,这就是为什么可预测的可靠供应商能够在竞争中获得主要优势并与大客户建立长期盈利关系的原因。
威胁 4:缺乏跨部门协作
稳定性改进通常涉及到解决复杂问题以识别会直接影响变异性的关键因素。解决此类问题通常需要生产、质量和设计等多个部门的协作。这些部门通常对稳定性问题有不同的看法。
为了改进这种情况,每个部门都可能会尝试实施各自的专门解决方案,不同团队的解决方案将有差异。通常,这些解决方案包括 Excel 文件,其中包含尚未在公司范围内验证的计算和方法,这可能会降低凝聚力。
幸运的是,Minitab Engage 是一款经过精心设计的绝佳解决方案,可帮助组织以协作方式构建改进和创新计划并借助问题解决工具和久经验证的项目管理方法执行这些计划。 收起阅读 »
然而,制造过程中通常有多个连续的步骤。即使一个步骤出现轻微偏差也可能影响整条生产线。为了帮助您更好地理解制造稳定性,本篇文章将:
1. 探索对改进生产稳定性起阻碍作用的常见威胁
2. 介绍如何克服这些威胁
3. 使您能够使用 Minitab Engage™运行自己的改进项目
让我们从制造稳定性的简要概述开始。
什么是生产稳定性?
生产稳定性是组织在任何给定时间段内保持其生产水平的能力。
什么是精益制造稳定性?
在精益制造中,稳定性一词用于描述可以使用相同的材料、设备和人员重复进行的生产过程。如果拥有稳定的过程,则将在可预测的时间范围内以最少的浪费支持高质量的输出。稳定性与变异相反,变异会对上述能力产生负面影响。
如何改进制造业中的生产稳定性
下面,我们将概述一些对稳定性的常见威胁,以及为贵组织解决这些威胁的方法。
威胁 1:标准化与人性
跨团队产生想法、合作开发数据驱动型解决方案以及使用强健的方法来识别变异源都需要经过验证的标准化工具。
不幸的是,人类的一些自然倾向会给团队带来问题和混淆:
• 在定义问题和范围之前跳转到解决方案。
• 在完成当前项目并解决手头问题之前,过快地转移到下一个问题。
• 主要基于主观臆测(而不是数据和铁证)提出潜在的解决方案。
• 开始分析数据而不检查其质量(包括数据的收集和测量方式)。
为了避免这些常见的缺陷,实施具有久经验证的可靠记录的方法将有助于团队分享共同的观点。例如,为了帮助您有效地解决复杂问题,DMAIC 方法具有以下标准化阶段:定义、测量、分析、改进和控制。它将问题划分为更便于管理的较小阶段,并使用包含多种强大工具的工具箱。我们最新的端到端改进解决方案 Minitab Engage 中提供了 DMAIC 以及其他问题解决方法。
确保项目遍历方法的所有步骤需要遵循一定的准则。幸运的是,Minitab Engage 通过阶段审查和审批、控制台报告和电子邮件通知随时跟踪您的项目。
威胁 2:公差
通常不可能完全消除过程中的变异。难以管理的紧公差通常会导致组织的最终成本增加。如果(在设计阶段)从一开始就没有充分考虑到这种威胁,制造厂家将难以实现其预期绩效。
随着供应链在全球范围内不断扩张,供应商力求完成更大的订单,供应商排名的一个关键标准是是否有能力保持在关键参数的规格限内。
威胁 3:稳定性 = 竞争优势
公司不断鼓励其供应商更好地控制其过程的稳定性。每当不稳定性在供应商之间传递并最终在客户之间传递时,因此导致的成本就会增加。在制造过程中很晚才检测到缺陷,这就是为什么可预测的可靠供应商能够在竞争中获得主要优势并与大客户建立长期盈利关系的原因。
威胁 4:缺乏跨部门协作
稳定性改进通常涉及到解决复杂问题以识别会直接影响变异性的关键因素。解决此类问题通常需要生产、质量和设计等多个部门的协作。这些部门通常对稳定性问题有不同的看法。
为了改进这种情况,每个部门都可能会尝试实施各自的专门解决方案,不同团队的解决方案将有差异。通常,这些解决方案包括 Excel 文件,其中包含尚未在公司范围内验证的计算和方法,这可能会降低凝聚力。
幸运的是,Minitab Engage 是一款经过精心设计的绝佳解决方案,可帮助组织以协作方式构建改进和创新计划并借助问题解决工具和久经验证的项目管理方法执行这些计划。 收起阅读 »
五大工具教材-MSA(初级版)
五大工具教材-MSA(初级版)
在 Minitab 中进行扩展量具 R&R 研究
量具 R&R 研究可以告诉您测量系统生成的数据是否值得信赖。遗憾的是,严格的数据要求和其他限制可能会让量具 R&R 研究难以进行分析,并可能无法解释所有重要因子。Minitab 中的扩展量具 R&R 工具能够使这些障碍成为过去。
量具 R&R 研究可以告诉您什么?
• 您的测量系统是否足够灵敏?
• 您的测量工具是否一致?
• 进行测量的人是否一致?
扩展量具 R&R 能提供哪些额外优势?
• 不仅要分析部件和操作员,还要分析多达八个其他因子。
• 甚至不完整的数据也可以进行分析(不平衡研究)。
• 包括固定或随机因子,获得更好的灵活性。
在量具 R&R 研究中包含两个以上的因子
通常,量具 R&R 研究只关注两个因子:部件和操作员。但是如果您知道其他因子也会影响您的测量系统呢?如果您不纳入这些因子,则将永远无法了解它们对测量变异性有多大影响,以及您的测量系统可能看起来比实际情况更好还是更差。Minitab 的扩展量具 R&R 能让您纳入最多八个额外的因子,用于调查并评估所有可能影响测量系统的因子。
例如
因为他们在繁忙的生产车间工作,检验人员担心生产速度的变化会影响他们的测量能力。加入生产线速度作为量具研究的因子,揭示出生产线速度变化对测量的影响甚至超出他们的预期。
以不完整或不平衡的数据进行量具 R&R
量具 R&R 研究可以要求严格的“平衡”设计,尽管实际上数据的收集通常并不完美。也许在研究中让操作员将所有部件测量相同的次数并不可行,或者可能一些测量数据已经丢失。扩展量具 R&R 允许您分析测量系统,即使有这样不平衡的数据,也无需手动计算来解释丢失的数据。
包括固定或随机因子以获取更高的灵活性
在量具研究中,如果您有意选择了一定的兴趣级别(比如最有经验和最缺乏经验的操作员),则该因子是固定的。如果您随机选择了级别来代表总体,则该因子为随机。常见量具研究会在所有因子均为随机的基础上计算结果。但将固定因子视为随机因子可能导致过度或低估其重要性。
扩展量具 R&R 允许您指明哪些因子是固定的,哪些是随机的,以便更好更妥当地评估您的测量系统。
例如
审核显示,退回精密铣削设施的大部分不合规格部件可追溯到两名经验最少的检验员。为了更好的理解该问题,质量经理希望能重点关注这些特定操作员后续的量具研究。因为人工挑选的这些操作员无法反应出随机抽样,所以在分析该研究时,经理将这一因子指定为固定因子。
MINITAB 让量具 R&R 更简单
如果您尚未利用 Minitab 的强大功能从数据中获取最大价值,请立即下载功能完备的 Minitab 30 天免费试用版。
本文最初出现在Minitab博客上。
收起阅读 »
量具 R&R 研究可以告诉您什么?
• 您的测量系统是否足够灵敏?
• 您的测量工具是否一致?
• 进行测量的人是否一致?
扩展量具 R&R 能提供哪些额外优势?
• 不仅要分析部件和操作员,还要分析多达八个其他因子。
• 甚至不完整的数据也可以进行分析(不平衡研究)。
• 包括固定或随机因子,获得更好的灵活性。
在量具 R&R 研究中包含两个以上的因子
通常,量具 R&R 研究只关注两个因子:部件和操作员。但是如果您知道其他因子也会影响您的测量系统呢?如果您不纳入这些因子,则将永远无法了解它们对测量变异性有多大影响,以及您的测量系统可能看起来比实际情况更好还是更差。Minitab 的扩展量具 R&R 能让您纳入最多八个额外的因子,用于调查并评估所有可能影响测量系统的因子。
例如
因为他们在繁忙的生产车间工作,检验人员担心生产速度的变化会影响他们的测量能力。加入生产线速度作为量具研究的因子,揭示出生产线速度变化对测量的影响甚至超出他们的预期。
以不完整或不平衡的数据进行量具 R&R
量具 R&R 研究可以要求严格的“平衡”设计,尽管实际上数据的收集通常并不完美。也许在研究中让操作员将所有部件测量相同的次数并不可行,或者可能一些测量数据已经丢失。扩展量具 R&R 允许您分析测量系统,即使有这样不平衡的数据,也无需手动计算来解释丢失的数据。
包括固定或随机因子以获取更高的灵活性
在量具研究中,如果您有意选择了一定的兴趣级别(比如最有经验和最缺乏经验的操作员),则该因子是固定的。如果您随机选择了级别来代表总体,则该因子为随机。常见量具研究会在所有因子均为随机的基础上计算结果。但将固定因子视为随机因子可能导致过度或低估其重要性。
扩展量具 R&R 允许您指明哪些因子是固定的,哪些是随机的,以便更好更妥当地评估您的测量系统。
例如
审核显示,退回精密铣削设施的大部分不合规格部件可追溯到两名经验最少的检验员。为了更好的理解该问题,质量经理希望能重点关注这些特定操作员后续的量具研究。因为人工挑选的这些操作员无法反应出随机抽样,所以在分析该研究时,经理将这一因子指定为固定因子。
MINITAB 让量具 R&R 更简单
如果您尚未利用 Minitab 的强大功能从数据中获取最大价值,请立即下载功能完备的 Minitab 30 天免费试用版。
本文最初出现在Minitab博客上。
收起阅读 »
测量系统一致性分析 | 这个汤真的那么辣吗?
熊妈妈已经忍无可忍了。最近一次关于她做的汤有多辣的争论以张牙舞爪而结束,而且把小女孩吓坏了。
熊妈妈认为问题出在小女孩身上。自从有了金凤花姑娘之后,所有人都无法就任何事情达成一致。床不是太软就是太硬。粥不是太烫就是太凉。今晚,金凤花姑娘抱怨汤太辣,熊爸爸抱怨汤不够辣。
为了使家庭恢复安宁,熊妈妈觉得小女孩需要离开。但是,每当熊妈妈提到这点时,熊爸爸就会跑过去为金凤花姑娘辩护。熊妈妈需要使用数据来为自己辩护,她明白该怎么做:使用一种名为“属性一致性分析”的测量系统分析。熊妈妈知道,使用 Minitab中的“协助”会使事情变得简单容易。
首先,她煮了六份汤。在其中的三份汤中,熊妈妈仅添加了足够的胡椒粉和香料,使汤美味但不会太辣。她在其余三份汤中加了过量的辣椒酱。
接着,熊妈妈使用 Minitab来设置、收集和分析数据,她希望确定为什么家庭成员如此频繁地出现意见不一致。
设置属性一致性分析
选择协助 > 测量系统分析 (MSA)…
“协助”显示一个决策树,该决策树中包括用于“评价”数据的 MSA。
熊妈妈打算让每个家庭成员都品尝六份不同的汤,并让他们评价是好(“好喝!”)还是差(“难喝!”)。每个评价者对每份汤都品尝 4 次,因此熊妈妈不仅能够查看不同检验者的意见是否一致,还能查看每个检验者每次品尝后的评价是否一致。
但是,她的数据收集计划能够满足此分析的需要吗?单击“属性一致性工作表”下面的“更多…”即可显示一列需要检查的要求。例如,“协助”建议评价者对相同数量的好和差项目进行评分,还建议至少有 3 个评价者,熊妈妈的计划中涵盖了这两项要求。
现在,熊妈妈确信她的计划非常恰当。她单击“返回”,然后单击“属性一致性工作表”并按如下所示填写对话框:
在单击“确定”之后,Minitab 将针对每个评价者和每份汤生成一组(共四个)随机试验,并创建一个匹配的数据表。
Minitab 还允许打印一整套随时可用的数据收集表单(每个试验和评价者有一份对应的表单)。
接着,熊妈妈加热这六份汤,并让每个检验者按照 Minitab 所指定的随机顺序对每份汤品尝四次。然后,她只需将结果输入到其数据表的相应列中就可以了:
分析数据
将结果输入到工作表中之后,熊妈妈可以继续进行分析。返回到协助 > 测量系统分析 (MSA)…,但这一次的目标是分析数据,而不是设置研究:
按如上所示填写对话框,单击“确定”。Minitab 将生成所有输出,熊妈妈需要使用这些输出来为自己辩护。
汇总报告显示,总体而言,家庭成员正确识别汤辛辣程度的正确率仅为 75%。按评价者计算的准确度百分比显示每个评价者对汤进行识别的准确度。熊妈妈和熊宝宝的得分最高,他们的准确度分别为 95.8% 和 87.5%。熊爸爸的准确度为 79.2%,不算太低。
但是,金凤花姑娘的准确度为 37.5%,很低。
“协助”的准确度报告为熊妈妈提供了有关每个评价者表现的具体细节。准确度报告右侧的按评价者计算的准确度百分比图和标准图显示,在三头熊中,每头熊都非常擅长识别美味的汤,但是,金凤花姑娘正确识别出美味的汤的概率不到 20%。
“协助”还有另外两个输出——“误分类报告”和“报告卡”。
证据在汤里
通过属性一致性分析的结果,可以清楚地判定有关汤辣不辣的大多数不一致源自何处,以及(按照熊妈妈的观点)不一致应当在何处终结。使用由“协助”创建的简单图形,甚至连熊爸爸也可以轻松看出,金凤花姑娘对汤的评价分歧可能会导致家庭成员产生冲突。
无论您喜欢清淡的汤还是喜欢超辣的汤,您都已经成功完成了此测量系统分析。您已了解如何创建属性一致性分析工作表,以及如何分析您收集的数据以使用“协助”来确定评价者在何处一致,在何处不一致。 收起阅读 »
熊妈妈认为问题出在小女孩身上。自从有了金凤花姑娘之后,所有人都无法就任何事情达成一致。床不是太软就是太硬。粥不是太烫就是太凉。今晚,金凤花姑娘抱怨汤太辣,熊爸爸抱怨汤不够辣。
为了使家庭恢复安宁,熊妈妈觉得小女孩需要离开。但是,每当熊妈妈提到这点时,熊爸爸就会跑过去为金凤花姑娘辩护。熊妈妈需要使用数据来为自己辩护,她明白该怎么做:使用一种名为“属性一致性分析”的测量系统分析。熊妈妈知道,使用 Minitab中的“协助”会使事情变得简单容易。
首先,她煮了六份汤。在其中的三份汤中,熊妈妈仅添加了足够的胡椒粉和香料,使汤美味但不会太辣。她在其余三份汤中加了过量的辣椒酱。
接着,熊妈妈使用 Minitab来设置、收集和分析数据,她希望确定为什么家庭成员如此频繁地出现意见不一致。
设置属性一致性分析
选择协助 > 测量系统分析 (MSA)…
“协助”显示一个决策树,该决策树中包括用于“评价”数据的 MSA。
熊妈妈打算让每个家庭成员都品尝六份不同的汤,并让他们评价是好(“好喝!”)还是差(“难喝!”)。每个评价者对每份汤都品尝 4 次,因此熊妈妈不仅能够查看不同检验者的意见是否一致,还能查看每个检验者每次品尝后的评价是否一致。
但是,她的数据收集计划能够满足此分析的需要吗?单击“属性一致性工作表”下面的“更多…”即可显示一列需要检查的要求。例如,“协助”建议评价者对相同数量的好和差项目进行评分,还建议至少有 3 个评价者,熊妈妈的计划中涵盖了这两项要求。
现在,熊妈妈确信她的计划非常恰当。她单击“返回”,然后单击“属性一致性工作表”并按如下所示填写对话框:
在单击“确定”之后,Minitab 将针对每个评价者和每份汤生成一组(共四个)随机试验,并创建一个匹配的数据表。
Minitab 还允许打印一整套随时可用的数据收集表单(每个试验和评价者有一份对应的表单)。
接着,熊妈妈加热这六份汤,并让每个检验者按照 Minitab 所指定的随机顺序对每份汤品尝四次。然后,她只需将结果输入到其数据表的相应列中就可以了:
分析数据
将结果输入到工作表中之后,熊妈妈可以继续进行分析。返回到协助 > 测量系统分析 (MSA)…,但这一次的目标是分析数据,而不是设置研究:
按如上所示填写对话框,单击“确定”。Minitab 将生成所有输出,熊妈妈需要使用这些输出来为自己辩护。
汇总报告显示,总体而言,家庭成员正确识别汤辛辣程度的正确率仅为 75%。按评价者计算的准确度百分比显示每个评价者对汤进行识别的准确度。熊妈妈和熊宝宝的得分最高,他们的准确度分别为 95.8% 和 87.5%。熊爸爸的准确度为 79.2%,不算太低。
但是,金凤花姑娘的准确度为 37.5%,很低。
“协助”的准确度报告为熊妈妈提供了有关每个评价者表现的具体细节。准确度报告右侧的按评价者计算的准确度百分比图和标准图显示,在三头熊中,每头熊都非常擅长识别美味的汤,但是,金凤花姑娘正确识别出美味的汤的概率不到 20%。
“协助”还有另外两个输出——“误分类报告”和“报告卡”。
证据在汤里
通过属性一致性分析的结果,可以清楚地判定有关汤辣不辣的大多数不一致源自何处,以及(按照熊妈妈的观点)不一致应当在何处终结。使用由“协助”创建的简单图形,甚至连熊爸爸也可以轻松看出,金凤花姑娘对汤的评价分歧可能会导致家庭成员产生冲突。
无论您喜欢清淡的汤还是喜欢超辣的汤,您都已经成功完成了此测量系统分析。您已了解如何创建属性一致性分析工作表,以及如何分析您收集的数据以使用“协助”来确定评价者在何处一致,在何处不一致。 收起阅读 »
EXCEL版MSA分析
不能使用专用软件,可以使用excel版做的MSA分析。密码5314046
优思学院|测量系统分析(MSA)中的偏倚和线性是什么?
原发表于优思学院知乎号
测量系统分析(MSA)是六西格玛和汽车工业行动小组 (AIAG) 的一个重要工具,一般来说,当我们利用一个量具去测量某一事物时,优思学院认为我们首先关注的是量具的分辩率,接着是量具的准确性(就是偏倚和线性度),最后就是测量的变异度(测量的精准度)。
偏倚和线性度
偏倚(Bias):观察到的测量平均值(在可重复性条件下进行试验)与参考值之间的差异;历史上称为准确性。偏差在测量系统的工作范围内的单个点上进行评估和表示。
线性度(Linearity):在测量系统的预期工作范围内偏置误差的差异。换句话说,线性表示操作范围内多个独立偏差误差的相关性。
偏倚是您的测量值与实际值的比较,而线性度是评估测量值在测量系统的工作范围内的准确度。
如果对量具的偏差和线性度有怀疑,你可以预先分析一下:
*选择几个零件(要分布到较极端的操作范围)
*每个零件都要进行测量(使用你要研究的量具每个零件至少测量10次,要随机进行)
Minitab中的关于偏倚和线性的研究
同学提问:
(zhuanlan.zhihu.com/p/438423133)
这是使用Minitab去研究偏倚和线性的方法,软件会导出以上这种结果。
首先,量具在各个参考值都存在偏差(Bias),而且非常明显,在量具偏倚的结果里显示所有参考尺寸的P值都小于0.05。例如,对于5.13的样件,平均偏差为0.157583。
线性(Linearity)方面,正如散点图中的正斜线所标识的那样。不同参考值的偏差都不一致,表明测量系统也有线性问题(P = 0.00)。
测量的精准度
当量具的准确度被确认后,我们便会进一步关注测量的变异度。
测量系统分析(MSA)是六西格玛绿带/黑带培训的其中一部分,测量的变异度在今天越来越受重视,因为以往我们一直都忽略这个很关键的东西,经常假定自己的量测没有任何问题,或者影响很轻微。
假设,供应商送货给你们的工厂,供应商有他们的QA测量检查,你们的工厂也有IQC,为什么老是出现质量问题而要退货呢,其中一个被忽略的情况是,大家的测量系统不同,测量的变异不同,测量系统分析(MSA)可以提供分析的工具,解决类似的问题。
收起阅读 »
测量系统分析(MSA)是六西格玛和汽车工业行动小组 (AIAG) 的一个重要工具,一般来说,当我们利用一个量具去测量某一事物时,优思学院认为我们首先关注的是量具的分辩率,接着是量具的准确性(就是偏倚和线性度),最后就是测量的变异度(测量的精准度)。
偏倚和线性度
偏倚(Bias):观察到的测量平均值(在可重复性条件下进行试验)与参考值之间的差异;历史上称为准确性。偏差在测量系统的工作范围内的单个点上进行评估和表示。
线性度(Linearity):在测量系统的预期工作范围内偏置误差的差异。换句话说,线性表示操作范围内多个独立偏差误差的相关性。
偏倚是您的测量值与实际值的比较,而线性度是评估测量值在测量系统的工作范围内的准确度。
如果对量具的偏差和线性度有怀疑,你可以预先分析一下:
*选择几个零件(要分布到较极端的操作范围)
*每个零件都要进行测量(使用你要研究的量具每个零件至少测量10次,要随机进行)
Minitab中的关于偏倚和线性的研究
同学提问:
六西格玛中的MSA,量具的线性偏倚,用minitab分析后得到下图。求详解。请问这张图意味着什么?
(zhuanlan.zhihu.com/p/438423133)
这是使用Minitab去研究偏倚和线性的方法,软件会导出以上这种结果。
首先,量具在各个参考值都存在偏差(Bias),而且非常明显,在量具偏倚的结果里显示所有参考尺寸的P值都小于0.05。例如,对于5.13的样件,平均偏差为0.157583。
线性(Linearity)方面,正如散点图中的正斜线所标识的那样。不同参考值的偏差都不一致,表明测量系统也有线性问题(P = 0.00)。
测量的精准度
当量具的准确度被确认后,我们便会进一步关注测量的变异度。
测量系统分析(MSA)是六西格玛绿带/黑带培训的其中一部分,测量的变异度在今天越来越受重视,因为以往我们一直都忽略这个很关键的东西,经常假定自己的量测没有任何问题,或者影响很轻微。
假设,供应商送货给你们的工厂,供应商有他们的QA测量检查,你们的工厂也有IQC,为什么老是出现质量问题而要退货呢,其中一个被忽略的情况是,大家的测量系统不同,测量的变异不同,测量系统分析(MSA)可以提供分析的工具,解决类似的问题。
收起阅读 »
检测过程需要做PFMEA分析吗?怎样分析?
在制造过程的设计中,总是要在制造工序间设置单独的检测步骤,这些检测步骤也是一个流程图的组成部分,例如,一个零件在焊接完毕后,对其部质量进行进行超声波检测;也可能是对其上游多个操作过程的综合探测,例如在智能音响中的所有声学零件组装成一个声学模组后,要进行声学项目的检测(还不是产品最终检测),我们把这样的检测过程叫做专检过程。
下图是一套产品过程流程图片断的示例,红色部分为检测过程。
我们知道,PFMEA是以产品过程流程图作为分析基础的,那么其中的检测过程需要做PFMEA分析吗?怎样分析它们的失效模式和失效起因呢?我们只研究它们的探测度或只做MSA可以吗?
这是在业界争议比较多的问题,本文就尝试展开讨论一下,供大家参考。
首先,为了避免再产生不必要的争议,我们先参考一下在2020年在汽车行业发布的新版AIAG-VDA FMEA手册(以下简称“FMEA手册”),其中在该书的3.1.2条“ PFMEA项目识别和边界”中有这么一段话:
工厂内会影响产品质量且可考虑进行PFMEA分析的过程包括:接收过程、零件和材料储存、产品和材料交付、制造、装配、包装、标签、成品运输、储存、维护过程、检测过程以及返工和返修过程等。
可见,在新版的FMEA手册中,检测过程是需要做PFMEA的,然而FMEA手册中却没有给出具体的方法和案例。
我们再看FMEA手册中3.5.3条关于“当前探测控制(DC)”的描述:
定义-当前探测控制是指在产品离开过程或发运给顾客前,通过自动或手动方法探测是否存在失效起因或失效模式。
如下图所示:
可见,对位于操作过程下游的检测过程来说,它既是产品制造过程流程图中需要做PFMEA的一个步骤,同时也可以看作是对前一个或多个操作过程的失效模式的探测。
二者并不矛盾,也并不重复,它们的作用和目的是不同的!作者建议我们先要对操作过程的当前探测措施和探测度进行分析、评价以及优化,在确定不再需要进一步优化之后,再单独对该检测过程进行PFMEA的分析,以便输出对检测过程的控制措施,从而减少测量误差和误判率!
我们先了解一下操作过程的探测措施。
它分为对失效起因的探测和对失效模式的探测,但是在实际的生产线和生产过程的设计时,人们往往不喜欢寻求防止失效起因的出现的预防措施,或者发现失效起因的探测措施,而是习惯于寻求对失效模式的探测,也就是我们常吐槽的“事后检验”、“死后验尸”,这似乎已经成为了一种天经地义的事情!这其实是一种非常落后的质量控制理念!通过下图,从同一个焊接过程中,我们可以全面了解这几种控制理念和方法:
从上图中可以看出,对于焊接、热处理、铸造、电镀、注塑等特殊过程,相当多的特性,如机械性能,是不能通过对产品的检测而得知的,这就必须识别出失效起因,对失效起因采取预防或者探测措施。即使是可以进行事后检测的产品,一旦发现不合格,也是一种浪费,因此,评价一个探测措施,我们需要分为这样几种情况:
对失效起因的探测,好于对失效模式的探测;在工位内失效模式的探测,好于下游工位的探测;仪器探测,好于人工目测;机器探测,好于人工探测;防错探测,好于一般机器/仪器探测。在FMEA手册的探测度D的打分指导中就是遵循此理念,读者可自行查阅。
因此,在对当前探测措施进行优化时,我们就要按上述“档位”做出改变,也就是升级为比当前更加先进的探测方法,这也是衡量一个过程设计是否先进的重要依据之一。一旦一个探测方法被确定下来,这个检测过程就形成了,我们就要对它加以管理,包括研究它的失效模式、失效起因,以及输出对它的控制计划。
那么怎样分析检测过程的PFMEA呢?它与MSA分析有什么关系呢?
我们还是使用FMEA手册中的失效链:
下面我们来探讨一下如何进行检测过程的PFMEA分析。
首先,我们要明确一个检测过程的功能是什么,很显然,执行检测,就是为了要把产品(注:在此处也包括零件、半成品,以下同)中的不合格的挑选出来,同时把合格的流到后面的工序当中去,因此,一个检测过程的失效模式应当是:把不合格的产品当作了合格的产品(接收不合格)、把合格的产品当作了不合格的产品(拒收合格),还可能在检测时把产品损坏了,例如特性的改变、损伤等。
它的失效影响和严重度S怎样分析呢?
如果是把不合格产品判断为合格产品,这相当于被检特性所对应的加工过程的失效模式和失效影响,例如,一个机加工过程,尺寸过大是这个加工过程的一个失效模式,可能会造成后续不能装配,如果它的专检工序失效,这个尺寸过大的零件就会被放行,同样也会造成后续不能进行装配。
如果是把合格产品判断为不合格产品,就会产生误报警,造成不必要的生产线停线事故。一家管理成熟的工厂都会有快速反应规则,包括生产线暂停运行,例如,如果是所检特性是一个关键特性,只要发现一次或几次问题,则会造成产线的暂停,这时S为7-8这个程度(请读者自行查阅一下FMEA手册的S打分指导);如果是一个次要特性,则只有达到一定数量或比例后才使生产线暂停,所以要看所检特性的重要度。
如果是因为检测而造成产品的损坏,这要根据受到影响的特性的重要度来确定S的值,例如检测过程损伤的是产品的表面质量,S仅仅是3-4。
如何分析检测过程的失效起因?
检测过程的影响因素,不同于加工过程的4M1E(人、机、料、法、环),而是SWIPE: S-标准、方法,W-工件,I-仪器/量具,P-测量者或者测量程序,E-测量环境。
总结以上分析,我们可以得到检测过程PFMEA失效分析的通用结构形式:
如何进行检测过程PFMEA的风险分析与控制措施的优化?
这是基于检测过程的当前预防措施和探测措施进行的分析和评价,同样也有着各自的Occurrence 和Detection。
预防措施是针对失效的起因采取的,对于检测过程,就是上述展开的SWIPE因素。
关于测量的方法(S)和发生频度(O)。当前的预防措施一般是原自于其他产品同类检测过程使用过的、已经证明是可靠的检测方法,一般是做成检测指导书的形式。分析和评价的目的是确认现有检测方法(检测指导书)是否会导致产生较高的测量误差或损伤。具体可以从这几个方面考虑:
• 是否分析过设计要求?
• 是否考虑过产品加工过程的特点(易出问题的地方)?
• 测量原理或过程是否与产品的运行过程和客户的使用工况相匹配?
• 测量方法是否存在产生较大测量误差或产生产品损伤的可能?
• 是否做过不同方法的MSA的分析和结果(测量误差)的对比?等等。
在设计一个检测过程时,如果这些方面没有充分研究过,则就有可能产生较大的测量误差,这也是确保一种检测方法可靠的预防控制措施。
检测过程失效起因发生频度O的打分,我们完全可以参考FMEA手册中的“过程的潜在频度O”的打分指导,例如,如果检测过程完全是一键控制式的自动化测量,且被测产品的定位也是自动化定位,那么关于方法这个因素的O就1分;如果完全是手工测量,例如使用卡尺或者目测,则要看检测方法指导书上有没有确定性、明确的、图文并茂的规定。
下面是作者在之前企业工作时遇到的一个典型案例。一个板金零件需要测量它的角度α,如下图所示,由于板金件在折弯机上折弯时,下面的工装支架产生了松动,使得两端的角度α1和α2不一致,如果不在检测指导书中规定一个明确的测量位置,则就会存在很大的重复性误差(即同一检验员使用同一把量具,也会产生不一致的结果)。
对于被测量的工件(W),其实这也与测量方法有关系。只要其特性不会随着时间的推移而发生变化,就不会影响测量的结果,而有些则是会随着时间而发生变化的,例如,零件的平面度,如果存在内应力,它会在加工完毕后随着应力的释放而发生变化;塑料件的尺寸会随着储存环境温度的变化而变化;电容的漏电量,不同时间是有变化的;压力(水压、气压)试验时压力随时间衰退,等等,这些特性的变化,就会大大影响测量结果,会产生较大的误判。
对于这样的被测量对象,我们必须采取相应的预防控制措施,即在测量方法中规定好测量的时间限制、补偿的系数等,否则,就会影响测量的结果。对于一般的特性稳定的产品工件,这个因素,是不打O值的。
测量的仪器/量具(I)和测量人员/程序(P)及它们的O值。 量具与测量者是两个重要的测量误差来源,对于量具来说,它的细分因素包括量具、试验台(平整度、是否有减震措施等)、测量设备和量检具出厂时的精度和稳定性(随使用环境因素变化)、夹具(夹紧力、夹持位置等);对于测量人员来说,是否在上岗前进行过专业的培训和资质的认证,以及是否经常轮换(会产生较大的再现性误差)等。
以上这些因素,在设计一个测量过程时,要事先充分考虑,并进行一一的策划与确认,采取相应的预防控制措施,例如,在三座标测量室中,应有温度控制措施,对于测量/试验台,应增加减振措施,对于量具的出厂精度,应依据要测量的零件设计精度要求(例如分辨率为公差范围的1/10以上),并对这些细分因素进行MSA的分析或者进行方差分析来对比研究,选择测量误差最小的方式。
关于这两个因素的O值打分,我们可以根据检测过程的MSA分析中量具和测量者的误差分量,再结合FMEA手册中的O值打分指导来进行打分。下面是如何将MSA的分析结果转化为O值的评价理论依据和示例:
下图是一个基准值为XT,偏倚为B,精度为σm的测量系统的一系列测量值所构成的分布(假设为正态),当我们研究量具的影响时,可以通过研究量具能力和GRR来获得单纯的量具偏倚(B)和重复性误差(σe),同理,当我们研究测量者之间或者量具之间的误差时,我们则使用再现性误差(σo)。
我们可以通过查寻或者通过统计软件计算正态累积概率函数来获得误判的类型和概率。
例如,一个测量系统,它测量一个零件的长度。经过测量系统分析得知,其偏倚B = 0.05,R&R的标准差也是0.05。如果测量一个基准值为0.4的零件长度,它的规格为0.6 – 1.0,那么有多大的概率产生误判?
对该结果的解释:虽然这个零件的基准值(0.4)在规格范围以外,是不合格的,但是,由于存在测量误差,理论上存在0.135%的误判风险(不合格判为合格)。在FMEA手册的过程潜在频度O(备选)打分指导中,这属于O值5-6的程度。
关于控制措施的优化,先看主要误差的类型,如果是偏倚而且恒定的,则可以采用补偿,否则,就需要矫正或者更换新量具;如果是精度误差较大,先看这个量具的出厂说明或制造标准中的理论测量精度,如果这个理论精度也达不到产品的测量要求(例如分辨率为公差范围的1/10以上),那么就应更换精度更高的量具类型,如果是因为磨损老化导致,则进行修理、矫正,或者更换。
对于测量环境(W)。测量环境对测量结果的影响,要看测量的产品和特性的类型,例如机械加工件,可能会对环境温度有较高的要求,如果是一个声学产品,则需要对环境噪声有极高的要求,需要在专门的、远离车间环境的听音室中进行检测。这些影响因素,在设计一个测量过程时要考虑、策划,并采取必要的预防措施。
检测过程的探测(D)
检测过程本身对应的是操作过程的失效模式探测,而检测过程自己的探测措施所要针对的则是对检测误差的发现机会和能力。我们怎样才能及时、有效地探测到一个检测过程(测量系统)产生的误差呢?这包括:对测量者的考核(频次、内容、标准)、对量具的校准(频次及机构)、测量系统分析MSA(指标、标准、频次、方法)等等,例如,这些类型的活动一次也没有做,则D应当为10分。
对检测过程的探测措施的优化包括提升校准/MSA的频次、增加样品的数量、改进抽样方案,以及执行这些活动计划是通过人工提醒,还是自动化提醒的方式等等。
综上所述,研究一个检测过程,实际上包括了MSA工作,且把MSA分析的结果应用于改进和优化检测过程。在业界的MSA培训和学习时,存在一种不好的习惯,就是只注重分析那几个测量系统的统计指标(偏倚、线性、稳定性、重复性、再现性),而忽视了对测量系统的构成(影响)因素的识别,忽视了把MSA统计指标应用于系统因素的进一步分析和改善上,其实这才是MSA的真正目的。
那么,有人会产生一个疑问:我们对检测过程进行MSA分析不就行了吗?为什么还要进行PFMEA呢?
对检测过程进行PFMEA分析,与单纯的MSA还是不一样的,检测过程PFMEA是面向整条产线上的所有检测过程,通过分析它们的S、O、D来确定是否需要优化(AP),怎样优化,优化完成后,再制定针对检测过程各影响因素的控制计划,用来管控这个检测过程不出现过大的测量误差,这才是对检测过程进行PFMEA分析的最终目的,这也是通常容易被忽视了的!这个控制计划就包括:是否做MSA分析,做哪些MSA指标,以及做MSA的频次,因此检测过程的PFMEA要比MSA高一个层次。下表是检测过程控制计划一个示例。
检测过程的PFMEA与MSA的关系,见下图所示。
收起阅读 »
下图是一套产品过程流程图片断的示例,红色部分为检测过程。
我们知道,PFMEA是以产品过程流程图作为分析基础的,那么其中的检测过程需要做PFMEA分析吗?怎样分析它们的失效模式和失效起因呢?我们只研究它们的探测度或只做MSA可以吗?
这是在业界争议比较多的问题,本文就尝试展开讨论一下,供大家参考。
首先,为了避免再产生不必要的争议,我们先参考一下在2020年在汽车行业发布的新版AIAG-VDA FMEA手册(以下简称“FMEA手册”),其中在该书的3.1.2条“ PFMEA项目识别和边界”中有这么一段话:
工厂内会影响产品质量且可考虑进行PFMEA分析的过程包括:接收过程、零件和材料储存、产品和材料交付、制造、装配、包装、标签、成品运输、储存、维护过程、检测过程以及返工和返修过程等。
可见,在新版的FMEA手册中,检测过程是需要做PFMEA的,然而FMEA手册中却没有给出具体的方法和案例。
我们再看FMEA手册中3.5.3条关于“当前探测控制(DC)”的描述:
定义-当前探测控制是指在产品离开过程或发运给顾客前,通过自动或手动方法探测是否存在失效起因或失效模式。
如下图所示:
可见,对位于操作过程下游的检测过程来说,它既是产品制造过程流程图中需要做PFMEA的一个步骤,同时也可以看作是对前一个或多个操作过程的失效模式的探测。
二者并不矛盾,也并不重复,它们的作用和目的是不同的!作者建议我们先要对操作过程的当前探测措施和探测度进行分析、评价以及优化,在确定不再需要进一步优化之后,再单独对该检测过程进行PFMEA的分析,以便输出对检测过程的控制措施,从而减少测量误差和误判率!
我们先了解一下操作过程的探测措施。
它分为对失效起因的探测和对失效模式的探测,但是在实际的生产线和生产过程的设计时,人们往往不喜欢寻求防止失效起因的出现的预防措施,或者发现失效起因的探测措施,而是习惯于寻求对失效模式的探测,也就是我们常吐槽的“事后检验”、“死后验尸”,这似乎已经成为了一种天经地义的事情!这其实是一种非常落后的质量控制理念!通过下图,从同一个焊接过程中,我们可以全面了解这几种控制理念和方法:
从上图中可以看出,对于焊接、热处理、铸造、电镀、注塑等特殊过程,相当多的特性,如机械性能,是不能通过对产品的检测而得知的,这就必须识别出失效起因,对失效起因采取预防或者探测措施。即使是可以进行事后检测的产品,一旦发现不合格,也是一种浪费,因此,评价一个探测措施,我们需要分为这样几种情况:
对失效起因的探测,好于对失效模式的探测;在工位内失效模式的探测,好于下游工位的探测;仪器探测,好于人工目测;机器探测,好于人工探测;防错探测,好于一般机器/仪器探测。在FMEA手册的探测度D的打分指导中就是遵循此理念,读者可自行查阅。
因此,在对当前探测措施进行优化时,我们就要按上述“档位”做出改变,也就是升级为比当前更加先进的探测方法,这也是衡量一个过程设计是否先进的重要依据之一。一旦一个探测方法被确定下来,这个检测过程就形成了,我们就要对它加以管理,包括研究它的失效模式、失效起因,以及输出对它的控制计划。
那么怎样分析检测过程的PFMEA呢?它与MSA分析有什么关系呢?
我们还是使用FMEA手册中的失效链:
下面我们来探讨一下如何进行检测过程的PFMEA分析。
首先,我们要明确一个检测过程的功能是什么,很显然,执行检测,就是为了要把产品(注:在此处也包括零件、半成品,以下同)中的不合格的挑选出来,同时把合格的流到后面的工序当中去,因此,一个检测过程的失效模式应当是:把不合格的产品当作了合格的产品(接收不合格)、把合格的产品当作了不合格的产品(拒收合格),还可能在检测时把产品损坏了,例如特性的改变、损伤等。
它的失效影响和严重度S怎样分析呢?
如果是把不合格产品判断为合格产品,这相当于被检特性所对应的加工过程的失效模式和失效影响,例如,一个机加工过程,尺寸过大是这个加工过程的一个失效模式,可能会造成后续不能装配,如果它的专检工序失效,这个尺寸过大的零件就会被放行,同样也会造成后续不能进行装配。
如果是把合格产品判断为不合格产品,就会产生误报警,造成不必要的生产线停线事故。一家管理成熟的工厂都会有快速反应规则,包括生产线暂停运行,例如,如果是所检特性是一个关键特性,只要发现一次或几次问题,则会造成产线的暂停,这时S为7-8这个程度(请读者自行查阅一下FMEA手册的S打分指导);如果是一个次要特性,则只有达到一定数量或比例后才使生产线暂停,所以要看所检特性的重要度。
如果是因为检测而造成产品的损坏,这要根据受到影响的特性的重要度来确定S的值,例如检测过程损伤的是产品的表面质量,S仅仅是3-4。
如何分析检测过程的失效起因?
检测过程的影响因素,不同于加工过程的4M1E(人、机、料、法、环),而是SWIPE: S-标准、方法,W-工件,I-仪器/量具,P-测量者或者测量程序,E-测量环境。
总结以上分析,我们可以得到检测过程PFMEA失效分析的通用结构形式:
如何进行检测过程PFMEA的风险分析与控制措施的优化?
这是基于检测过程的当前预防措施和探测措施进行的分析和评价,同样也有着各自的Occurrence 和Detection。
预防措施是针对失效的起因采取的,对于检测过程,就是上述展开的SWIPE因素。
关于测量的方法(S)和发生频度(O)。当前的预防措施一般是原自于其他产品同类检测过程使用过的、已经证明是可靠的检测方法,一般是做成检测指导书的形式。分析和评价的目的是确认现有检测方法(检测指导书)是否会导致产生较高的测量误差或损伤。具体可以从这几个方面考虑:
• 是否分析过设计要求?
• 是否考虑过产品加工过程的特点(易出问题的地方)?
• 测量原理或过程是否与产品的运行过程和客户的使用工况相匹配?
• 测量方法是否存在产生较大测量误差或产生产品损伤的可能?
• 是否做过不同方法的MSA的分析和结果(测量误差)的对比?等等。
在设计一个检测过程时,如果这些方面没有充分研究过,则就有可能产生较大的测量误差,这也是确保一种检测方法可靠的预防控制措施。
检测过程失效起因发生频度O的打分,我们完全可以参考FMEA手册中的“过程的潜在频度O”的打分指导,例如,如果检测过程完全是一键控制式的自动化测量,且被测产品的定位也是自动化定位,那么关于方法这个因素的O就1分;如果完全是手工测量,例如使用卡尺或者目测,则要看检测方法指导书上有没有确定性、明确的、图文并茂的规定。
下面是作者在之前企业工作时遇到的一个典型案例。一个板金零件需要测量它的角度α,如下图所示,由于板金件在折弯机上折弯时,下面的工装支架产生了松动,使得两端的角度α1和α2不一致,如果不在检测指导书中规定一个明确的测量位置,则就会存在很大的重复性误差(即同一检验员使用同一把量具,也会产生不一致的结果)。
对于被测量的工件(W),其实这也与测量方法有关系。只要其特性不会随着时间的推移而发生变化,就不会影响测量的结果,而有些则是会随着时间而发生变化的,例如,零件的平面度,如果存在内应力,它会在加工完毕后随着应力的释放而发生变化;塑料件的尺寸会随着储存环境温度的变化而变化;电容的漏电量,不同时间是有变化的;压力(水压、气压)试验时压力随时间衰退,等等,这些特性的变化,就会大大影响测量结果,会产生较大的误判。
对于这样的被测量对象,我们必须采取相应的预防控制措施,即在测量方法中规定好测量的时间限制、补偿的系数等,否则,就会影响测量的结果。对于一般的特性稳定的产品工件,这个因素,是不打O值的。
测量的仪器/量具(I)和测量人员/程序(P)及它们的O值。 量具与测量者是两个重要的测量误差来源,对于量具来说,它的细分因素包括量具、试验台(平整度、是否有减震措施等)、测量设备和量检具出厂时的精度和稳定性(随使用环境因素变化)、夹具(夹紧力、夹持位置等);对于测量人员来说,是否在上岗前进行过专业的培训和资质的认证,以及是否经常轮换(会产生较大的再现性误差)等。
以上这些因素,在设计一个测量过程时,要事先充分考虑,并进行一一的策划与确认,采取相应的预防控制措施,例如,在三座标测量室中,应有温度控制措施,对于测量/试验台,应增加减振措施,对于量具的出厂精度,应依据要测量的零件设计精度要求(例如分辨率为公差范围的1/10以上),并对这些细分因素进行MSA的分析或者进行方差分析来对比研究,选择测量误差最小的方式。
关于这两个因素的O值打分,我们可以根据检测过程的MSA分析中量具和测量者的误差分量,再结合FMEA手册中的O值打分指导来进行打分。下面是如何将MSA的分析结果转化为O值的评价理论依据和示例:
下图是一个基准值为XT,偏倚为B,精度为σm的测量系统的一系列测量值所构成的分布(假设为正态),当我们研究量具的影响时,可以通过研究量具能力和GRR来获得单纯的量具偏倚(B)和重复性误差(σe),同理,当我们研究测量者之间或者量具之间的误差时,我们则使用再现性误差(σo)。
我们可以通过查寻或者通过统计软件计算正态累积概率函数来获得误判的类型和概率。
例如,一个测量系统,它测量一个零件的长度。经过测量系统分析得知,其偏倚B = 0.05,R&R的标准差也是0.05。如果测量一个基准值为0.4的零件长度,它的规格为0.6 – 1.0,那么有多大的概率产生误判?
对该结果的解释:虽然这个零件的基准值(0.4)在规格范围以外,是不合格的,但是,由于存在测量误差,理论上存在0.135%的误判风险(不合格判为合格)。在FMEA手册的过程潜在频度O(备选)打分指导中,这属于O值5-6的程度。
关于控制措施的优化,先看主要误差的类型,如果是偏倚而且恒定的,则可以采用补偿,否则,就需要矫正或者更换新量具;如果是精度误差较大,先看这个量具的出厂说明或制造标准中的理论测量精度,如果这个理论精度也达不到产品的测量要求(例如分辨率为公差范围的1/10以上),那么就应更换精度更高的量具类型,如果是因为磨损老化导致,则进行修理、矫正,或者更换。
对于测量环境(W)。测量环境对测量结果的影响,要看测量的产品和特性的类型,例如机械加工件,可能会对环境温度有较高的要求,如果是一个声学产品,则需要对环境噪声有极高的要求,需要在专门的、远离车间环境的听音室中进行检测。这些影响因素,在设计一个测量过程时要考虑、策划,并采取必要的预防措施。
检测过程的探测(D)
检测过程本身对应的是操作过程的失效模式探测,而检测过程自己的探测措施所要针对的则是对检测误差的发现机会和能力。我们怎样才能及时、有效地探测到一个检测过程(测量系统)产生的误差呢?这包括:对测量者的考核(频次、内容、标准)、对量具的校准(频次及机构)、测量系统分析MSA(指标、标准、频次、方法)等等,例如,这些类型的活动一次也没有做,则D应当为10分。
对检测过程的探测措施的优化包括提升校准/MSA的频次、增加样品的数量、改进抽样方案,以及执行这些活动计划是通过人工提醒,还是自动化提醒的方式等等。
综上所述,研究一个检测过程,实际上包括了MSA工作,且把MSA分析的结果应用于改进和优化检测过程。在业界的MSA培训和学习时,存在一种不好的习惯,就是只注重分析那几个测量系统的统计指标(偏倚、线性、稳定性、重复性、再现性),而忽视了对测量系统的构成(影响)因素的识别,忽视了把MSA统计指标应用于系统因素的进一步分析和改善上,其实这才是MSA的真正目的。
那么,有人会产生一个疑问:我们对检测过程进行MSA分析不就行了吗?为什么还要进行PFMEA呢?
对检测过程进行PFMEA分析,与单纯的MSA还是不一样的,检测过程PFMEA是面向整条产线上的所有检测过程,通过分析它们的S、O、D来确定是否需要优化(AP),怎样优化,优化完成后,再制定针对检测过程各影响因素的控制计划,用来管控这个检测过程不出现过大的测量误差,这才是对检测过程进行PFMEA分析的最终目的,这也是通常容易被忽视了的!这个控制计划就包括:是否做MSA分析,做哪些MSA指标,以及做MSA的频次,因此检测过程的PFMEA要比MSA高一个层次。下表是检测过程控制计划一个示例。
检测过程的PFMEA与MSA的关系,见下图所示。
收起阅读 »
谈谈测量系统分析的另一种方法VDA5
你知道吗,测量系统分析方法其实不仅仅只是我们常见的AIAG的《MSA 参考手册》中的那些方法,还有VDA 5。
我们都知道,在I区,坏零件永远判为坏零件,在III区,好零件永远判为好零件。当测量值落在规格限附近时,即II区时候,可能对零件做出错误的决策,如合格的判为不合格,不合格的判为合格。
MSA给了一个概念性的方向:改进生产过程来减少过程变差,尽量不要让零件落在区域II,或者改进测量系统,以减少II区的面积,来减少做出错误决策的风险。如何决定II区,MSA手册并没有给出明确的指导。
但在VDA5中,给出了科学的方法。如果供应商的测量值在规范内,而你的测量值在规范外,是判定合格还是不合格呢。和MSA手册里类似,落在区域3,证明合格,落在区域4,证明不合格,落在区域5,属于不确定区,无法判断合格还是不合格。关键的是,VDA5中给出了方法来确定不确定区-参照ISO14253-1来做确定不确定区域(即5区)。
VDA5符合国际标准GUM和VIM的要求,术语和定义与国际标准保持一致。VDA5评估不确定度的方法分为A类不确定度和B类不确定度,结合现有在企业运用的MSA分析中的方法一,方法二或方法三的结果,将量具的分辨率,偏倚,测量标准件的重复性,测量工件的重复性,操作者间的再现性,均转化为不确定度的分量。
提出了处理线性,温度,被测件本身的不均一导致的不确定度
对于测量系统的验收,测量过程能力的证明,将测量结果应用于于产品符合性判断中,VDA5提出了非常有益的应用上的指导。
VDA5是一种简化的GUM的方法,将MSA的结果和GUM结合起来,程序简单,便于实践。它的一般程序如下图:
见附件 收起阅读 »
我们都知道,在I区,坏零件永远判为坏零件,在III区,好零件永远判为好零件。当测量值落在规格限附近时,即II区时候,可能对零件做出错误的决策,如合格的判为不合格,不合格的判为合格。
MSA给了一个概念性的方向:改进生产过程来减少过程变差,尽量不要让零件落在区域II,或者改进测量系统,以减少II区的面积,来减少做出错误决策的风险。如何决定II区,MSA手册并没有给出明确的指导。
但在VDA5中,给出了科学的方法。如果供应商的测量值在规范内,而你的测量值在规范外,是判定合格还是不合格呢。和MSA手册里类似,落在区域3,证明合格,落在区域4,证明不合格,落在区域5,属于不确定区,无法判断合格还是不合格。关键的是,VDA5中给出了方法来确定不确定区-参照ISO14253-1来做确定不确定区域(即5区)。
VDA5符合国际标准GUM和VIM的要求,术语和定义与国际标准保持一致。VDA5评估不确定度的方法分为A类不确定度和B类不确定度,结合现有在企业运用的MSA分析中的方法一,方法二或方法三的结果,将量具的分辨率,偏倚,测量标准件的重复性,测量工件的重复性,操作者间的再现性,均转化为不确定度的分量。
提出了处理线性,温度,被测件本身的不均一导致的不确定度
对于测量系统的验收,测量过程能力的证明,将测量结果应用于于产品符合性判断中,VDA5提出了非常有益的应用上的指导。
VDA5是一种简化的GUM的方法,将MSA的结果和GUM结合起来,程序简单,便于实践。它的一般程序如下图:
见附件 收起阅读 »
SJ5730粗糙度轮廓测量一体机在轴承行业的应用
轴承是制造业中关键的基础零部件,直接决定着重大装备和主机产品的性能、质量和可靠性,被誉为装备制造的“心脏”部件。
轴承运转的平稳性、噪声、发热、摩擦状况很大程度上取决于沟道和滚动体的制造精度。滚道一般多为圆弧形(或者类似圆弧),其深度可以达到数十毫米,一般的粗糙度仪由于量程过小,难以测到整个弧线的粗糙度,同时滚道圆弧轮廓的精确评价手段也不够,多数厂家对此类参数难以有效控制,产品质量难以提高。
针对此现状,中图仪器成功推出SJ5730粗糙度轮廓测量一体机。
仪器特点
一次性测出滚道的粗糙度和轮廓度,可以对任意位置的粗糙度进行选择评价。
案例解析:国内某著名轴承品牌。
SJ5730轴承实测图
下表为测量轴承滚道的粗糙度Ra和Pt值
Ra曲线
Pt曲线
仪器采用高精度衍射光栅测头,具有12mm的粗糙度测量范围,分辨率达到1nm。
一次测量可同时评定粗糙度及轮廓参数,能够灵活选取测量范围,显示计算Ra参数和Pt参数。
由上表测量结果可知,仪器的测量重复性好,多次测量结果偏差较小,能够满足客户对精密轴承检测的要求。
SJ5730粗糙度轮廓测量一体机能够满足轴承行业所有的测量需求,如内外套圈的密封槽形状(角度、倒角、槽深、槽宽等);各种滚子轴承的滚子和套圈母线的凸度、角度、曲线;滚针轴承、圆柱滚子轴承、直线轴承的滚动体和套圈的直线度;球轴承沟道的沟曲率半径;四点接触轴承的沟曲率半径等。
轴承行业在攻克高品质课题的过程中,离不开高精密测量仪器的支撑。中图仪器作为计量检测产品的专业厂商,给客户提供丰富的产品解决方案,应对不同客户多样性的测量需求,助力成就高品质产品制造。 收起阅读 »
原创 | 不谈SPC的Cp、Cpk都是耍流氓!
兑现承诺。
这个拿以前的资料整理的,完成速度比较快。
准确的说:计算Cpk还有第四个条件:过程稳态;这里在原文稍微点了下,没有强调。
下一篇《当Cp、Cpk遭遇单边公差?》,由于琐事缠身,更新时间不定。
Sol_Sun
2019/10/28 收起阅读 »
这个拿以前的资料整理的,完成速度比较快。
准确的说:计算Cpk还有第四个条件:过程稳态;这里在原文稍微点了下,没有强调。
下一篇《当Cp、Cpk遭遇单边公差?》,由于琐事缠身,更新时间不定。
Sol_Sun
2019/10/28 收起阅读 »
大数据时代下的质量管理与六西格玛
不管你承不承认,愿不愿意,大数据时代都将到来;
作为一名质量人,我们应当做好准备拥抱它的到来,而不是被它的到来带来的改变而抛弃。
下面请放开你的思想,畅所欲言:
1,大数据时代的到来会给质量管理带来什么变化?
2,大数据时代与六西格玛会擦除什么样的火花?
3,。。。。。。 收起阅读 »
作为一名质量人,我们应当做好准备拥抱它的到来,而不是被它的到来带来的改变而抛弃。
下面请放开你的思想,畅所欲言:
1,大数据时代的到来会给质量管理带来什么变化?
2,大数据时代与六西格玛会擦除什么样的火花?
3,。。。。。。 收起阅读 »
MSA GRR研究时两个普遍纠结的问题
文章原创:姜传武(John Jiang) 资深质量咨询&培训师
电话:18501797352,个人主页:http://www.jiangshi99.com/home/jiangchuanwu/?from=recommend
在我所讲的MSA课程中,我发现有两个问题,学员们每次都在纠结,它就是:
第一个问题:我们周期性地评价GRR时,是使用初次评价时的样本,还是当前过程的样本?
第二个问题:在PPAP时做的GRR是满意的,但是在量产很长一段时间后,再用当前产品做分析样本时,GRR指标又不好了,但是制造过程比当初更加稳定了,零件的变差减小了,所以不能就说测量系统的GRR是不满足要求的,测量系统不用改进!我们不能为了MSA而MSA,因为再提高测量精度,所用的成本太高了!
以上问题,我基本上保留原样,但是在给出正式的解答前,忍不住先反问一下:
在没有分析测量系统是否真的变坏了前,怎么能讲零件的变差变小了呢?用于分析零件变差的测量数据可信吗?
这个问题反映的其实是MSA的最基本的概念,甚至还涉及一些质量理念方面的东西,所以值得写一下,与大家分享和探讨。
在回答这个问题之前,必须首先要明确什么是GRR。GRR是测量系统中的精度误差,是MSA工作的一部分,是用测量值的标准差来估计的,它表示测量系统本身的测量误差大小。它在测量系统的所有影响因素没有显著变化的情况下是不变的,它的大小与用什么时候的样本也是没有关系的。
测量系统的精度是否满足测量要求呢?这就要把GRR值与要求进行比较,看一下测量系统满足测量要求的能力是否发生了变化。这才是进行测量系统评估的真正目的!
测量的目的不同,要求也就不同。通常情况下,我们把测量用于满足下面两类不同的目的:
第一类:用于产品检验,判断产品的特性是否合格,将GRR与特性公差比。测量要求就是测量系统能够区分合格与不合格;
第二类:进行统计分析,由于测量值由真实值和测量误差构成,这时的测量要求就是测量值之间的变差能够足以精确反映制造过程的实际总变差(表现为该过程所生产的零件特性的一致性),就要把GRR与测量值之间的变差进行比较,所占比例越小,则说明测量值越能反映实际的过程总变差。这类应用常见的有:SPC控制图、CPK、6SIGMA改善、STA(统计公差分析)等。
在MSA中,针对这两类应用的目的,规定了如下三个GRR的评价指标:
当测量值被用于第一类目的,即产品的检验、验收时,使用100(GRR/T),可见,大小只与测量系统本身的GRR和公差T有关,与用什么时候的样本是没有关系的,反映的是测量系统精度是否存在显著的绝对变化。
当测量值被用于第二类目的,即统计分析时,使用100(GRR/TV)和分类数ndc来评价。其中,TV是一个总变差,它是通过测量值(也叫观察值)来计算的,它总是或多或少地含有测量误差,即由两部分构成:真实的过程总变差(零件特性间的真实变差)和测量误差(GRR)。因此,TV是动态的,它随着零件特性之间的变差的变化而变化,当然,也会因GRR变化而变化。
一般情况下,在刚刚量产时,由于还可能存在着许多问题没有完全解决,零件特性间的变差会比较大,而随着量产时间的增加,问题逐渐解决,又做了一系列的持续改善,零件特性的一致性就会变得越来越好,这时σpart和TV就会变小!换句话讲,就是100(GRR/TV)和ndc会与我们用哪些样本来评价有关系,如果再使用当初的样本评价GRR,所计算出的这个结果就不能正确判断测量系统是否真正满足当前的测量要求了。如果硬要使用当初的样本,则会有如下可能的误导:
1. CPK很高,但可能是一派虚假的繁荣!或者SPC控制图上出现连续水平排列的点。但过程能力是否真的提高了,还是测量系统是否真的变差了,单从100(GRR/TV)和ndc上是看不出的;
2. CPK保持稳定,但可能是一个虚假的稳定,测量系统和实际过程能力可能同时都变差了!
3. 评价一项改善是否成功时,我们需要进行改善前、后的CPK对比,若使用当初的样本,则测量结果会显示没有成效或未达改善目标!因为测量系统的分辨率差,不能有效分辨出改善措施所带来的变化!
在以上基础上,我们可以对一开始的两个问题总结出以下GRR研究的策略:
1. 如果测量系统只用于检验产品,则可以使用任何时候的产品作为样本,只考察100(GRR/T)这个指标;
2. 如果测量系统同时还用于统计分析,则要讲究样本了。我们可以用以下步骤来做:
1) 从当前过程中抽取样本,这个样本应涵盖当前过程的所有5M1E过程因素的正常更替,如:换班次、换料批、修磨刀具等,怎样才能做到呢?这就需要时间来抽样!例如,把所用的不同样本分配到不同的班次、原材料批次中。
此时,需要注意的是:如果你没有足够的时间得到满足上述要求的样本,是可以从一个班次中抽样的,但是,从样本中计算出来的TV就不能很好地反映真实的过程的总变差(零件特性间的真实变差)!建议使用过程总变差的目标值来代替TV,可以从PPK计算公式中推导出来(此处略去公式和推导)。但是要注意:如果实际过程的性能还未达标,则我们评价的%GRR就相当于对测量系统满足期望目标的能力;如果过程性能实际上已经超过了PPK的目标要求,则此处%GRR的结果可能要高估了当前测量系统满足当前测量要求的真实能力,即100(GRR/TV)和ndc虚高!
2) 计算100(GRR/TV),并将结果与100(GRR/T)的结果进行对比。
a) 若100(GRR/TV)不满足要求(如大于10%),同时100(GRR/T)满足要求,该测量系统的精度没有发生显著下降,这是由于制造过程能力提高的结果,使得总变差TV变小的原因,但是事实是:测量系统已经不能满足对当前制造过程的统计分析的要求了!
到底需不需要改善呢?很多人在这个地方纠结!因为测量系统本身没有下降,要改善的话,可能要投入很多成本,例如更换高等级的测量仪器或自动化测量设备,会投入巨资的!这个时候就要看我们的质量管理的要求了,理论上讲,如果没有过程持续改善的测量需求,就没有必要改善测量系统,但此时要注意两点:
第一,当客户需要CPK报告时,你是否能够说服客户?
第二,为什么不对过程和产品进行持续改善?!客户有了更高的质量水平的要求、竞争对手有了更高的质量水平的表现,你还在停滞不前吗?很多时候,需要我们有战略观,战略就是要求我们不只是看到眼前所花的成本,而是要看到更长远、更大的范围内的风险和要求,从而保证战略总成本最低!
b) 若100(GRR/TV)是满足要求的,但是100(GRR/T)是不满足要求的,则说明测量系统并不是真正的好,与第一次GRR分析(当时是满足要求的)的时候相比,已经发生了显著的下降了,但其测量精度仍然能够满足当前制造过程的统计分析的要求。这时应当对测量系统进行改善了,最起码要满足检验的要求!若不改善,100(GRR/TV)也很可能会在下一次GRR研究前就不合要求了。
c) 若二者同时满足要求,则测量系统没有问题。
d) 若二者同时不满足要求,则毫无疑问,测量系统的精度已经绝对地变差了,必须要改善了。
总之,周期性进行的GRR分析,应当使用代表当前制造过程实际总变差的样本,并同时进行两种%GRR指标的对比分析,从而判断出两层涵义:
第一,测量系统的精度是否绝对地发生了显著变化;
第二,测量系统的精度是否满足当前过程的测量要求。
若没有足够的时间抽取代表当前过程的样本,则可以使用PPK目标值所对应的过程总变差来代替当前过程的TV,但这样做也不是最好的。
收起阅读 »
电话:18501797352,个人主页:http://www.jiangshi99.com/home/jiangchuanwu/?from=recommend
在我所讲的MSA课程中,我发现有两个问题,学员们每次都在纠结,它就是:
第一个问题:我们周期性地评价GRR时,是使用初次评价时的样本,还是当前过程的样本?
第二个问题:在PPAP时做的GRR是满意的,但是在量产很长一段时间后,再用当前产品做分析样本时,GRR指标又不好了,但是制造过程比当初更加稳定了,零件的变差减小了,所以不能就说测量系统的GRR是不满足要求的,测量系统不用改进!我们不能为了MSA而MSA,因为再提高测量精度,所用的成本太高了!
以上问题,我基本上保留原样,但是在给出正式的解答前,忍不住先反问一下:
在没有分析测量系统是否真的变坏了前,怎么能讲零件的变差变小了呢?用于分析零件变差的测量数据可信吗?
这个问题反映的其实是MSA的最基本的概念,甚至还涉及一些质量理念方面的东西,所以值得写一下,与大家分享和探讨。
在回答这个问题之前,必须首先要明确什么是GRR。GRR是测量系统中的精度误差,是MSA工作的一部分,是用测量值的标准差来估计的,它表示测量系统本身的测量误差大小。它在测量系统的所有影响因素没有显著变化的情况下是不变的,它的大小与用什么时候的样本也是没有关系的。
测量系统的精度是否满足测量要求呢?这就要把GRR值与要求进行比较,看一下测量系统满足测量要求的能力是否发生了变化。这才是进行测量系统评估的真正目的!
测量的目的不同,要求也就不同。通常情况下,我们把测量用于满足下面两类不同的目的:
第一类:用于产品检验,判断产品的特性是否合格,将GRR与特性公差比。测量要求就是测量系统能够区分合格与不合格;
第二类:进行统计分析,由于测量值由真实值和测量误差构成,这时的测量要求就是测量值之间的变差能够足以精确反映制造过程的实际总变差(表现为该过程所生产的零件特性的一致性),就要把GRR与测量值之间的变差进行比较,所占比例越小,则说明测量值越能反映实际的过程总变差。这类应用常见的有:SPC控制图、CPK、6SIGMA改善、STA(统计公差分析)等。
在MSA中,针对这两类应用的目的,规定了如下三个GRR的评价指标:
当测量值被用于第一类目的,即产品的检验、验收时,使用100(GRR/T),可见,大小只与测量系统本身的GRR和公差T有关,与用什么时候的样本是没有关系的,反映的是测量系统精度是否存在显著的绝对变化。
当测量值被用于第二类目的,即统计分析时,使用100(GRR/TV)和分类数ndc来评价。其中,TV是一个总变差,它是通过测量值(也叫观察值)来计算的,它总是或多或少地含有测量误差,即由两部分构成:真实的过程总变差(零件特性间的真实变差)和测量误差(GRR)。因此,TV是动态的,它随着零件特性之间的变差的变化而变化,当然,也会因GRR变化而变化。
一般情况下,在刚刚量产时,由于还可能存在着许多问题没有完全解决,零件特性间的变差会比较大,而随着量产时间的增加,问题逐渐解决,又做了一系列的持续改善,零件特性的一致性就会变得越来越好,这时σpart和TV就会变小!换句话讲,就是100(GRR/TV)和ndc会与我们用哪些样本来评价有关系,如果再使用当初的样本评价GRR,所计算出的这个结果就不能正确判断测量系统是否真正满足当前的测量要求了。如果硬要使用当初的样本,则会有如下可能的误导:
1. CPK很高,但可能是一派虚假的繁荣!或者SPC控制图上出现连续水平排列的点。但过程能力是否真的提高了,还是测量系统是否真的变差了,单从100(GRR/TV)和ndc上是看不出的;
2. CPK保持稳定,但可能是一个虚假的稳定,测量系统和实际过程能力可能同时都变差了!
3. 评价一项改善是否成功时,我们需要进行改善前、后的CPK对比,若使用当初的样本,则测量结果会显示没有成效或未达改善目标!因为测量系统的分辨率差,不能有效分辨出改善措施所带来的变化!
在以上基础上,我们可以对一开始的两个问题总结出以下GRR研究的策略:
1. 如果测量系统只用于检验产品,则可以使用任何时候的产品作为样本,只考察100(GRR/T)这个指标;
2. 如果测量系统同时还用于统计分析,则要讲究样本了。我们可以用以下步骤来做:
1) 从当前过程中抽取样本,这个样本应涵盖当前过程的所有5M1E过程因素的正常更替,如:换班次、换料批、修磨刀具等,怎样才能做到呢?这就需要时间来抽样!例如,把所用的不同样本分配到不同的班次、原材料批次中。
此时,需要注意的是:如果你没有足够的时间得到满足上述要求的样本,是可以从一个班次中抽样的,但是,从样本中计算出来的TV就不能很好地反映真实的过程的总变差(零件特性间的真实变差)!建议使用过程总变差的目标值来代替TV,可以从PPK计算公式中推导出来(此处略去公式和推导)。但是要注意:如果实际过程的性能还未达标,则我们评价的%GRR就相当于对测量系统满足期望目标的能力;如果过程性能实际上已经超过了PPK的目标要求,则此处%GRR的结果可能要高估了当前测量系统满足当前测量要求的真实能力,即100(GRR/TV)和ndc虚高!
2) 计算100(GRR/TV),并将结果与100(GRR/T)的结果进行对比。
a) 若100(GRR/TV)不满足要求(如大于10%),同时100(GRR/T)满足要求,该测量系统的精度没有发生显著下降,这是由于制造过程能力提高的结果,使得总变差TV变小的原因,但是事实是:测量系统已经不能满足对当前制造过程的统计分析的要求了!
到底需不需要改善呢?很多人在这个地方纠结!因为测量系统本身没有下降,要改善的话,可能要投入很多成本,例如更换高等级的测量仪器或自动化测量设备,会投入巨资的!这个时候就要看我们的质量管理的要求了,理论上讲,如果没有过程持续改善的测量需求,就没有必要改善测量系统,但此时要注意两点:
第一,当客户需要CPK报告时,你是否能够说服客户?
第二,为什么不对过程和产品进行持续改善?!客户有了更高的质量水平的要求、竞争对手有了更高的质量水平的表现,你还在停滞不前吗?很多时候,需要我们有战略观,战略就是要求我们不只是看到眼前所花的成本,而是要看到更长远、更大的范围内的风险和要求,从而保证战略总成本最低!
b) 若100(GRR/TV)是满足要求的,但是100(GRR/T)是不满足要求的,则说明测量系统并不是真正的好,与第一次GRR分析(当时是满足要求的)的时候相比,已经发生了显著的下降了,但其测量精度仍然能够满足当前制造过程的统计分析的要求。这时应当对测量系统进行改善了,最起码要满足检验的要求!若不改善,100(GRR/TV)也很可能会在下一次GRR研究前就不合要求了。
c) 若二者同时满足要求,则测量系统没有问题。
d) 若二者同时不满足要求,则毫无疑问,测量系统的精度已经绝对地变差了,必须要改善了。
总之,周期性进行的GRR分析,应当使用代表当前制造过程实际总变差的样本,并同时进行两种%GRR指标的对比分析,从而判断出两层涵义:
第一,测量系统的精度是否绝对地发生了显著变化;
第二,测量系统的精度是否满足当前过程的测量要求。
若没有足够的时间抽取代表当前过程的样本,则可以使用PPK目标值所对应的过程总变差来代替当前过程的TV,但这样做也不是最好的。
收起阅读 »
测量系统分析-线性偏倚分析
个人觉得不错,分享给大家。
为保证我们的测量系的准确性,我们生产过程中,要对测量系统进行测量系统分析,以了解测量系统的变差分量,确定这变差分量是否可接受以及做相应的改善。
以下我介绍一下测量系统分析中的线性偏倚分析,知识有限有不对的地方请多多指教。
决定要对某工序测量外形尺寸的测量系统做线性偏倚分析,此过程变差=0.01mm.要求测量系统偏小于过程变差的1/3.
一、数据收集:
1、 人员:经培训合格的操作人员1位;
2、 测量仪器:测量范围为(0~100)mm的A仪器;
3、 分析样品:取5个分析样品,使用高一级测量仪器测得量值分别为:
1mm、5 mm、10 mm、50 mm、100 mm。
4、 测量方法:测试人员,在重复性条件下,使用直接测量分析对5个样品测量15次,得到测量结果;
5、 分析环境:23℃,54%RH.
二、分析数据-使用MINITAB工具
1、把数据按MINITAB的数据格式,填入MINITAB工作表中:
2、使用MINITAB的量具线性和偏倚研究工具,计算出结果。
3、输出结果如下:
4、分析判定:
从上图与数据我们可判定,此测量系统存在显著的线性偏倚,但%偏倚都小于30%,所以对于此过程,此测量系的偏倚可接受;
1) 常量P=0.000<0.05, 斜率P=0.000<0.05,说明存在线性偏倚;
2) 图表与R-S=71.9%也证实了这一结论;
最大%偏倚=17.3%<30%,所在虽然此测量系统存在线性偏倚,但用于此过程是可接受的。不需要修正或改善。
如果需修正可使用此线性回归方程对测量结果进行有效的修正:
Y=1.00002X-0.000722.
收起阅读 »
为保证我们的测量系的准确性,我们生产过程中,要对测量系统进行测量系统分析,以了解测量系统的变差分量,确定这变差分量是否可接受以及做相应的改善。
以下我介绍一下测量系统分析中的线性偏倚分析,知识有限有不对的地方请多多指教。
决定要对某工序测量外形尺寸的测量系统做线性偏倚分析,此过程变差=0.01mm.要求测量系统偏小于过程变差的1/3.
一、数据收集:
1、 人员:经培训合格的操作人员1位;
2、 测量仪器:测量范围为(0~100)mm的A仪器;
3、 分析样品:取5个分析样品,使用高一级测量仪器测得量值分别为:
1mm、5 mm、10 mm、50 mm、100 mm。
4、 测量方法:测试人员,在重复性条件下,使用直接测量分析对5个样品测量15次,得到测量结果;
5、 分析环境:23℃,54%RH.
二、分析数据-使用MINITAB工具
1、把数据按MINITAB的数据格式,填入MINITAB工作表中:
2、使用MINITAB的量具线性和偏倚研究工具,计算出结果。
3、输出结果如下:
4、分析判定:
从上图与数据我们可判定,此测量系统存在显著的线性偏倚,但%偏倚都小于30%,所以对于此过程,此测量系的偏倚可接受;
1) 常量P=0.000<0.05, 斜率P=0.000<0.05,说明存在线性偏倚;
2) 图表与R-S=71.9%也证实了这一结论;
最大%偏倚=17.3%<30%,所在虽然此测量系统存在线性偏倚,但用于此过程是可接受的。不需要修正或改善。
如果需修正可使用此线性回归方程对测量结果进行有效的修正:
Y=1.00002X-0.000722.
收起阅读 »
MSA MINITAB 6图分析 详细
一、变异分量图(理想情况下)
贡献%<10%(方差分量/变异度),研究变异%<30%(量具变异/总变异),公差%(6*量具标准差/公差)<30%。
二、测量值样品图(理想情况下)
样本内部比较集中,说明测量的值变异较小。样本间波动大,说明样本选取覆盖了过程。
三、R图(理想情况下)
不能超出规格线,子组内变异较小,差异小。
四、测量值检验员(理想情况下)
箱形图看分布(直方图原理),差别小,均值近似在一条线上。
五、XBar图(理想情况下)
此处论坛疑问较多,实则与SPC处控制图无异,当我们选取样本时,最好要覆盖过程,10个数值,两三个在规格线外,两三个在规格线处,两三个在规格线内,即 MSA手册中的三个区。
I Bad parts will always be called bad(坏的就是坏的,怎么测都是坏的)
II Potential wrong decision can be made(可能好,可能坏)
III Good parts will always be called good(好的就是好的,怎么测都是好的)。
样本选取时为什么建议覆盖过程公差而不去覆盖过程变差,情况:当过程变差远远小于过程公差,此时若按过程变差选的话,所选的数据非常集中,一般情况下,测量系统分析的结果是分辨力不够。不合格。 10:1后(过程变差/10)<< 量具分辨力.
六、部件*操作员交互作用图(理想情况下)
表明员工与零件之间的关系怎样随着操作员的变化而变化,正常状况是每条线的形状一样。即没有交错。
欢迎补充
2017/7/27
4:15
收起阅读 »
贡献%<10%(方差分量/变异度),研究变异%<30%(量具变异/总变异),公差%(6*量具标准差/公差)<30%。
二、测量值样品图(理想情况下)
样本内部比较集中,说明测量的值变异较小。样本间波动大,说明样本选取覆盖了过程。
三、R图(理想情况下)
不能超出规格线,子组内变异较小,差异小。
四、测量值检验员(理想情况下)
箱形图看分布(直方图原理),差别小,均值近似在一条线上。
五、XBar图(理想情况下)
此处论坛疑问较多,实则与SPC处控制图无异,当我们选取样本时,最好要覆盖过程,10个数值,两三个在规格线外,两三个在规格线处,两三个在规格线内,即 MSA手册中的三个区。
I Bad parts will always be called bad(坏的就是坏的,怎么测都是坏的)
II Potential wrong decision can be made(可能好,可能坏)
III Good parts will always be called good(好的就是好的,怎么测都是好的)。
样本选取时为什么建议覆盖过程公差而不去覆盖过程变差,情况:当过程变差远远小于过程公差,此时若按过程变差选的话,所选的数据非常集中,一般情况下,测量系统分析的结果是分辨力不够。不合格。 10:1后(过程变差/10)<< 量具分辨力.
六、部件*操作员交互作用图(理想情况下)
表明员工与零件之间的关系怎样随着操作员的变化而变化,正常状况是每条线的形状一样。即没有交错。
欢迎补充
2017/7/27
4:15
收起阅读 »
喷漆附着力与零件表面清洁度的关系
在各种产品的表面处理工艺中, 喷漆与底材的附着力差,出现掉漆、起泡、划格法测试不合格的问题会经常出现。 而底材表面不干净,有油污、油尘、指纹等污染物是造成附着力不良的关键原因。而表面处理70%的不良都是在清洗过程造成的。由于清洗不彻底,清洗过后的零件表面容易残留油、脂、蜡、胶黏剂、指纹、残留的清洗剂等有机污染物。这些有机污染物的过量残留是影响后工序如焊接、喷涂效果的主要原因之一。
通过荧光激发法对零件表面进行检测,监控清洗后工件的清洁度,建立清洁度标准,可以避免因胶黏剂残留过量造成的喷涂附着力差、甚至喷涂不上的问题。
以汽车铭牌为例,汽车铭牌毛坯在加工过后通过贴膜来防止毛坯板刮花和二次污染。目前的贴膜方式有两种:第一种为静电吸附膜,第二种为丙烯酸胶黏剂(丙烯酸)粘合膜。粘合膜在撕掉后会有胶黏剂残留在毛坯板上,工程师认为这是造成后续工序中喷涂效果不好的主要原因,使喷涂涂层有附着不上或涂层脱落的风险。
相关测试仪器
SITA Cleanospector清洁度测试仪
以下为合格样品和不合格样品的比较
不合格样品(A样品)
合格样品(B样品)
通过比较A、B两样品的清洁度曲线可以发现:
A样品曲线平稳的地方为底材干净的部位,示值为5RFU左右;示值在中后部有波动,最大值达到了15RFU,说明此区域有胶黏剂残留。
B样品曲线一直平稳在5RFU左右,几乎没有波动,说明B样品这个板面清洁度很均匀,相对比较干净。
收起阅读 »
通过荧光激发法对零件表面进行检测,监控清洗后工件的清洁度,建立清洁度标准,可以避免因胶黏剂残留过量造成的喷涂附着力差、甚至喷涂不上的问题。
以汽车铭牌为例,汽车铭牌毛坯在加工过后通过贴膜来防止毛坯板刮花和二次污染。目前的贴膜方式有两种:第一种为静电吸附膜,第二种为丙烯酸胶黏剂(丙烯酸)粘合膜。粘合膜在撕掉后会有胶黏剂残留在毛坯板上,工程师认为这是造成后续工序中喷涂效果不好的主要原因,使喷涂涂层有附着不上或涂层脱落的风险。
相关测试仪器
SITA Cleanospector清洁度测试仪
以下为合格样品和不合格样品的比较
不合格样品(A样品)
合格样品(B样品)
通过比较A、B两样品的清洁度曲线可以发现:
A样品曲线平稳的地方为底材干净的部位,示值为5RFU左右;示值在中后部有波动,最大值达到了15RFU,说明此区域有胶黏剂残留。
B样品曲线一直平稳在5RFU左右,几乎没有波动,说明B样品这个板面清洁度很均匀,相对比较干净。
收起阅读 »
1分钟教你制作测量系统线性案例
某工厂检验员对某过程引进一套新测量系统,作用PPAP的一部分需要对测量系统的线性进行评价。
根据已文件化的过程变差描述,在测量系统的全部工作量程范围内选取了五个零件。通过对每个零件进行
全尺寸检验测量以确定其参考值,然后由主要操作者对每个零件测量12次。 在分析中,这些零件是附件抽取的.
数据如下:
基准值
2 4 6 8 10
测试数据
2.7 5.1 5.8 7.6 9.1
2.5 3.9 5.7 7.7 9.3
2.4 4.2 5.9 7.8 9.5
2.5 5 5.9 7.7 9.3
2.7 3.8 6 7.8 9.4
2.3 3.9 6.1 7.8 9.5
2.5 3.9 6 7.8 9.5
2.5 3.9 6.1 7.7 9.5
2.4 3.9 6.4 7.8 9.6
2.4 4 6.3 7.5 9.2
2.6 4.1 6 7.6 9.3
2.4 3.8 6.1 7.7 9.4
操作:
1, 6SQ统计--测量系统分析--线性
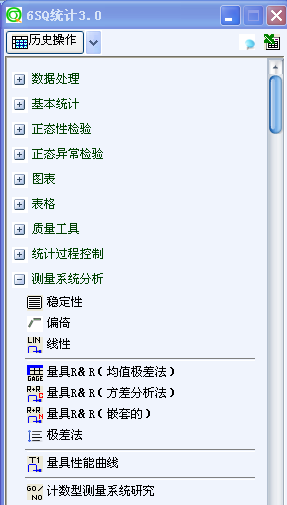
2, 分布选择基准值范围和数据范围
3,点确定,输出结果
线性百分率(斜率 * 100 的绝对值)是 13.2,这表示量具线性占整个过程变异的 13%。
Excel数据及案例
http://pan.baidu.com/s/1i5AXSRN
6SQ统计3.0企业版90天试用下载 http://pan.baidu.com/s/1i5AXSRN 收起阅读 »
根据已文件化的过程变差描述,在测量系统的全部工作量程范围内选取了五个零件。通过对每个零件进行
全尺寸检验测量以确定其参考值,然后由主要操作者对每个零件测量12次。 在分析中,这些零件是附件抽取的.
数据如下:
基准值
2 4 6 8 10
测试数据
2.7 5.1 5.8 7.6 9.1
2.5 3.9 5.7 7.7 9.3
2.4 4.2 5.9 7.8 9.5
2.5 5 5.9 7.7 9.3
2.7 3.8 6 7.8 9.4
2.3 3.9 6.1 7.8 9.5
2.5 3.9 6 7.8 9.5
2.5 3.9 6.1 7.7 9.5
2.4 3.9 6.4 7.8 9.6
2.4 4 6.3 7.5 9.2
2.6 4.1 6 7.6 9.3
2.4 3.8 6.1 7.7 9.4
操作:
1, 6SQ统计--测量系统分析--线性
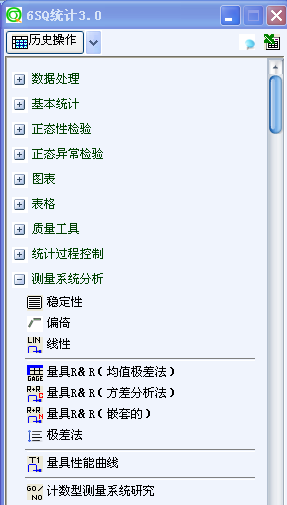
2, 分布选择基准值范围和数据范围
3,点确定,输出结果
线性百分率(斜率 * 100 的绝对值)是 13.2,这表示量具线性占整个过程变异的 13%。
Excel数据及案例
http://pan.baidu.com/s/1i5AXSRN
6SQ统计3.0企业版90天试用下载 http://pan.baidu.com/s/1i5AXSRN 收起阅读 »